- Home
- News
Essential Insights on Visual Checks for Electrical Equipment Safety and Efficiency
In today's fast-paced industrial environment, ensuring the safety and efficiency of electrical equipment is paramount. A recent report from the National Fire Protection Association (NFPA) highlights that approximately 13% of fires in commercial properties are caused by electrical failures. This alarming statistic underscores the importance of regular maintenance and inspection processes. Among these processes, conducting effective visual checks on electrical equipment is a fundamental practice that can significantly reduce the risk of equipment malfunction and enhance overall safety.
Furthermore, the International Electrotechnical Commission (IEC) suggests that a considerable number of electrical accidents can be prevented through routine inspections. Visual checks on electrical equipment not only help in identifying visible signs of wear and potential hazards but also play a crucial role in maintaining compliance with safety regulations. By adopting a proactive approach to visual inspections, organizations can protect their assets, ensure the safety of their personnel, and maintain operational efficiency in their electrical systems.
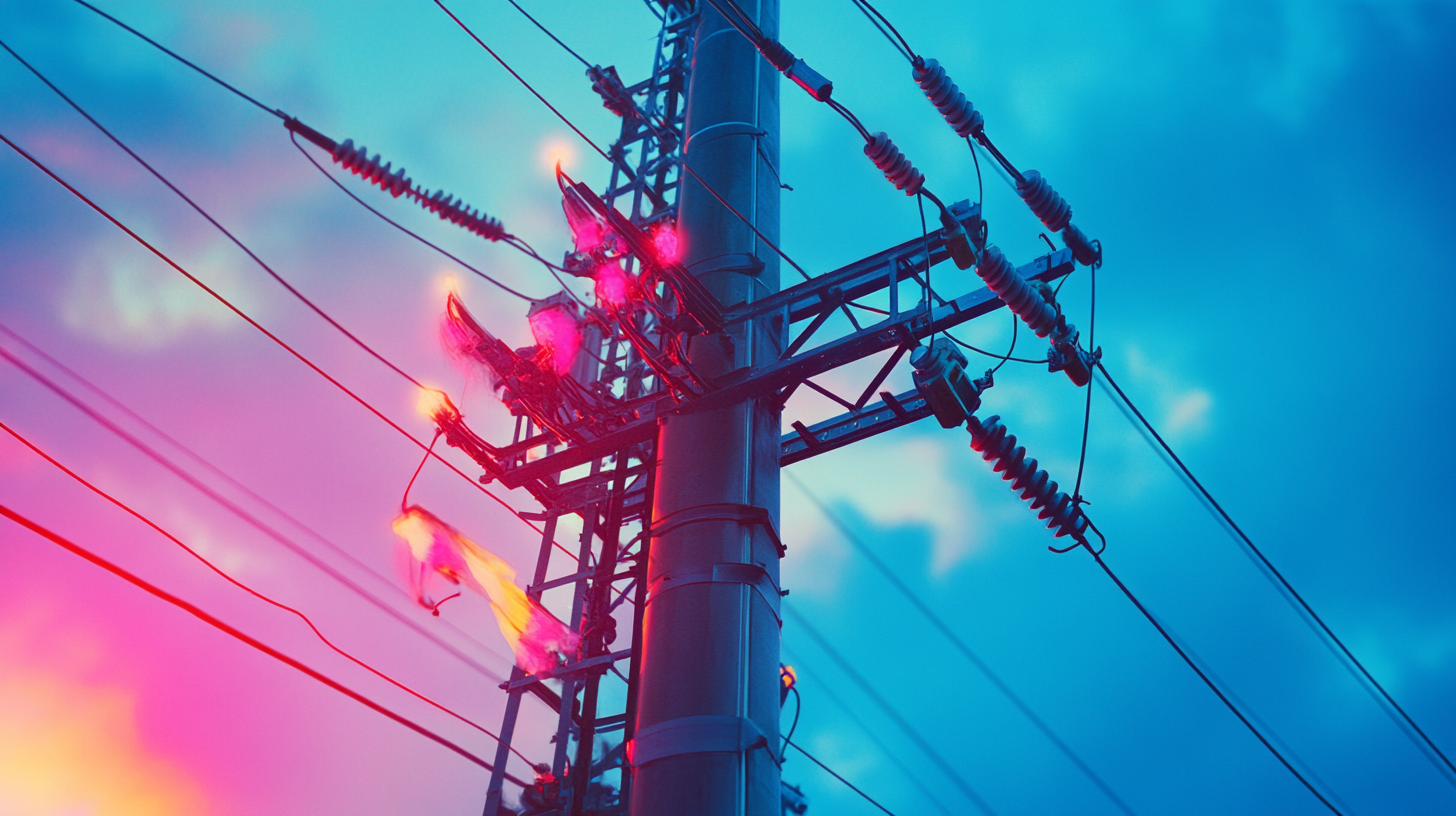
Importance of Routine Visual Inspections for Electrical Equipment
You know, keeping a close eye on our electrical equipment is super important for both safety and efficiency—especially these days when our infrastructure is changing fast and the demand for electricity is just skyrocketing. Recently, regulators have been calling out companies for not having strong enough inspection practices, especially in spots where wildfires are a real threat. Take Southern California Edison, for example. They've been under the microscope for not being quick enough with their inspections of transmission lines in risky areas. It really drives home how crucial those routine checks are when it comes to preventing disasters. Regular visual inspections can catch problems before they turn into major headaches, which is especially key now that our electrical systems often run at such high DC voltage levels. Higher voltages mean more risk, so having a solid inspection routine is a must. You know, studies actually show that doing these regular checks can really cut down the chances of equipment breakdowns—things we absolutely want to avoid, given that they can lead to hefty outages and dangerous situations. And let's be honest, using new tech like drones and AI for inspections is really changing the game in how effective and efficient these checks can be. On top of that, as the industry shifts toward more automated techniques, it’s still super important to keep up with traditional visual inspections. Companies like Penelec are already on it, doing their inspections consistently and setting up maintenance strategies to make sure things run smoothly—especially when demand hits its peak. With new standards coming up from organizations like NFPA, it’s clear that ongoing visual checks are vital for compliance and excellence in operations. By putting routine inspections front and center, organizations can really boost the safety and efficiency of their electrical systems, keeping both the infrastructure and the communities they serve a whole lot safer.
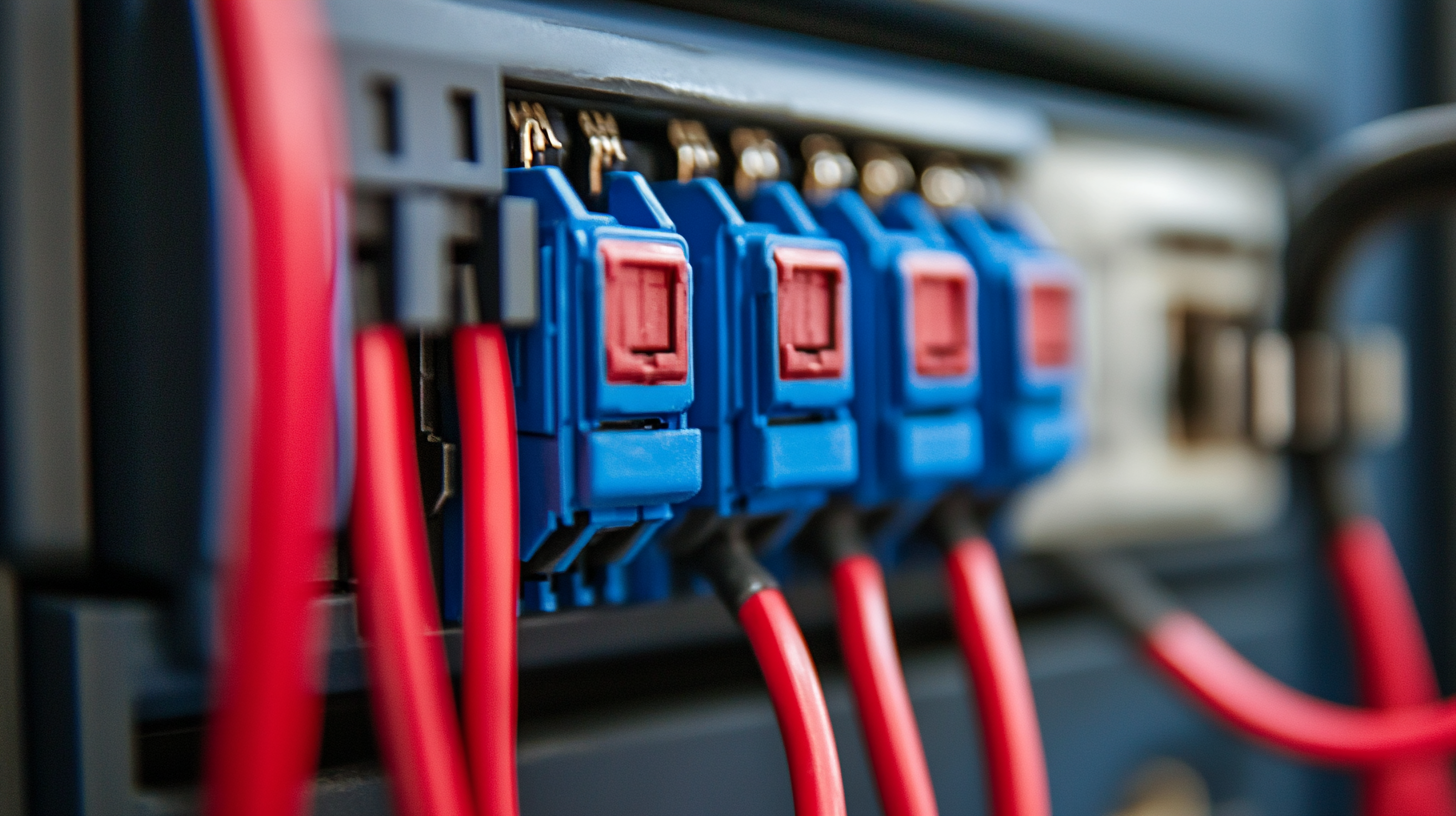
Key Indicators to Look for During Visual Checks
Hey there! So, when it comes to checking the safety and efficiency of electrical equipment, it's super important to really pay attention to some key signs. Inspectors need to look closely at the insulation condition—any signs of wear or degradation shouldn’t be ignored. If you spot any frayed wires or exposed conductors, that’s a serious safety hazard that needs to be fixed right away. And let’s not forget about the connections; making sure they’re tight and free of corrosion is essential because loose connections can really cause some overheating issues and might even lead to failures down the line.
Also, keep an eye out for any visible signs of overheating, like discoloration or melted parts. These usually mean the equipment is being pushed too hard, which can mess with its efficiency and how long it lasts. Plus, you really shouldn’t skip checking for dust and debris around vents and cooling systems—these little guys can seriously slow things down and could even lead to breakdowns over time.
Lastly, operators should take a good look at the overall structure of the equipment to make sure there aren’t any cracks or weird shapes in the housing. A solid, intact casing is key to keeping those internal components safe from the elements that could affect safety and performance. By keeping these factors in mind during visual inspections, organizations can really boost the reliability of their electrical systems and cut down on potential risks too!
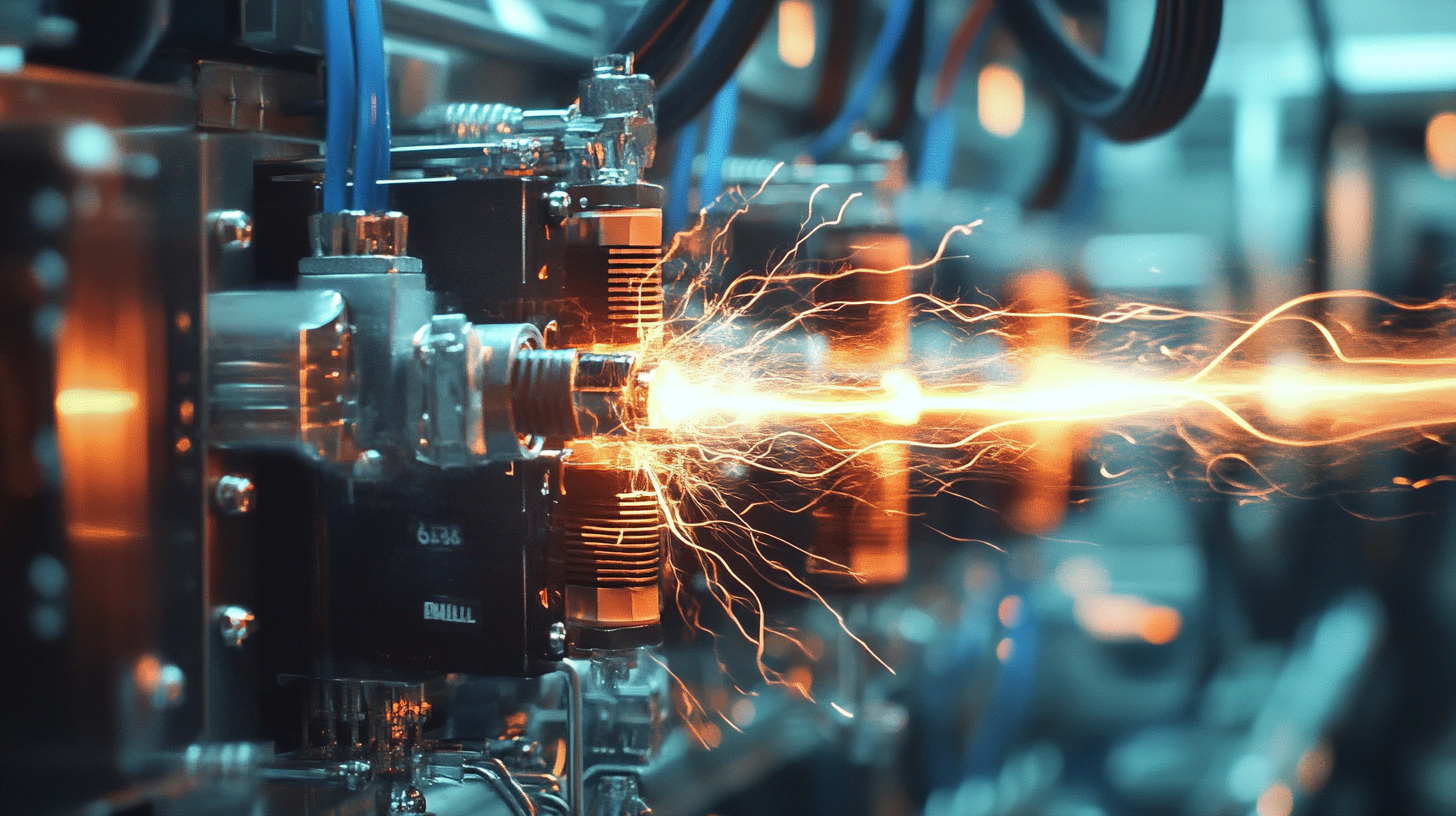
Common Issues Identified Through Visual Inspections
You know, visual inspections are really important for keeping electrical equipment safe and running smoothly. It's surprising how often these checks get overlooked! But honestly, they can uncover all sorts of issues that, if we catch them early, save us from some pretty nasty repair bills and keep everything running at its best. A biggie that often pops up during these inspections is wear and tear on cables and connections. Things like damaged insulation, frayed wires, or even loose connections can lead to short circuits or total equipment failure, which is definitely not something you want—it can even be dangerous!
And let’s not forget about the dust and grime. Over time, dirt can build up on electrical components and mess with their functioning. If we don’t keep things clean, we might end up with overheating issues or worse, electrical fires! So, making sure everything is tidy and free of junk should really be part of any safety game plan. Plus, those signs of corrosion on terminals and connectors? Yeah, they’re a red flag for reduced electrical conductivity, which means your equipment won’t work as efficiently. Regular visual checks help us catch these problems early on, so we can fix them before things get out of hand.
On top of all that, visual inspections are super important for spotting any unapproved repairs or modifications to the equipment. You know, stuff that could totally mess with safety certifications and create unsafe situations. By sticking to a regular schedule for these checks, companies can not only extend the life of their electrical systems but also foster a culture of safety and responsibility among the team. It’s just good practice, really!
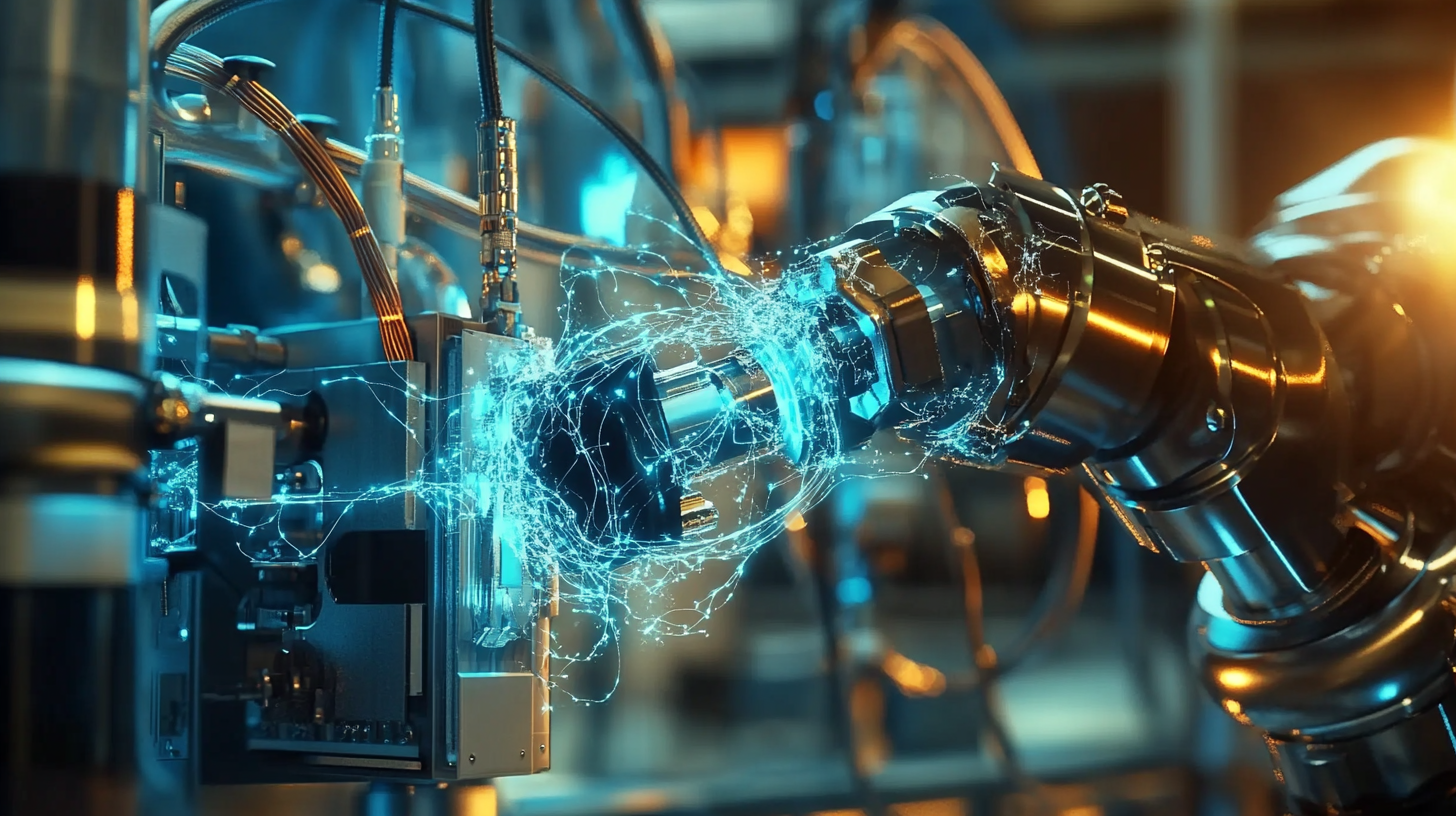
Best Practices for Conducting Effective Visual Checks
You know, doing visual checks on electrical equipment is super important for keeping things safe and running smoothly. When professionals take the time for regular inspections, it helps them catch potential problems early on, before they turn into major headaches. One of the best ways to go about these checks is to keep a detailed record of what’s been inspected. That way, it’s easier to see any changes that pop up over time and makes everyone accountable. Using customized checklists for different types of equipment can really speed things up, ensuring nothing crucial gets missed.
And let’s not forget about how cool technology is making things these days! Drones can totally shake up the whole inspection game. With high-res cameras, they can zip around large areas and spot any wear and tear that might slip through the cracks during manual checks. This not only keeps folks safe by minimizing the need for them to go into risky spots, but it also boosts the accuracy of the inspections. Pretty neat, right?
Plus, it’s super important to keep training staff on how to do these visual inspections effectively. When you invest in their education, they stay on top of the latest safety protocols and are much better at spotting those sneaky signs that something might be wrong with the equipment. By building a culture that emphasizes safety and eye for detail, organizations can really cut down on risks related to electrical equipment and overall, improve how efficiently things run.
Maintaining Electrical Equipment: When to Seek Professional Help
You know, when it comes to keeping electrical equipment running smoothly, knowing when to call in the pros is super important for both safety and efficiency. I mean, it's pretty startling to think that nearly 24% of all reported structure fires are linked to electrical failures, according to the National Fire Protection Association (NFPA). That really drives home how essential it is to do visual checks and get expert help when something doesn’t seem right. Sure, regular inspections can help spot issues like frayed wires or signs of corrosion and overload, but let's be honest—sometimes you need a trained professional to figure out the nitty-gritty and fix those problems the right way.
So, what are some signs that you really should call in the experts? Well, if you find yourself constantly tripping circuit breakers, hearing weird sounds from your equipment, or noticing any overheating, those are big red flags. The Electrical Safety Foundation International (ESFI) actually recommends that businesses bring in licensed electricians for preventative maintenance at least once a year. This not only helps to extend the life of your equipment but can save you from expensive downtimes and possible hazards. For instance, a report from the International Electrotechnical Commission (IEC) found that keeping up with maintenance can reduce operational costs by as much as 30%. That’s some serious savings, right?
And let’s not forget how complicated our modern electrical systems have become! With all these IoT devices and smart technology popping up everywhere, staying on top of the latest safety standards is more crucial than ever. That’s where the professionals come in—they've got the know-how to assess these systems thoroughly, making sure everything’s in line with the current regulations and practices. Plus, routine maintenance by skilled technicians not only protects your equipment but also keeps the entire electrical system in good shape. So, really, investing in professional help can save you a lot of trouble in the long run!