- Home
- News
5 Essential Tips for Ensuring Electrical Safety Testing Success
Ensuring electrical safety is paramount in today's technology-driven environment, as electrical failures can lead to catastrophic incidents such as fires, injuries, and even fatalities. According to the National Fire Protection Association (NFPA), electrical failures were a factor in an estimated 21,000 fires annually, causing millions in property damage and putting countless lives at risk. Therefore, implementing rigorous Testing Electrical Safety protocols is not just a regulatory requirement but a critical component of responsible business practices.
In light of these pressing concerns, organizations must prioritize effective electrical safety testing to mitigate potential hazards and ensure compliance with standards. The International Electrotechnical Commission (IEC) emphasizes the importance of regular testing, revealing that companies that adhere to established safety guidelines experience up to 75% fewer incidents in the workplace. By integrating well-structured testing procedures and empowering staff with essential safety knowledge, businesses can enhance their operational reliability and protect their most valuable asset—their people.
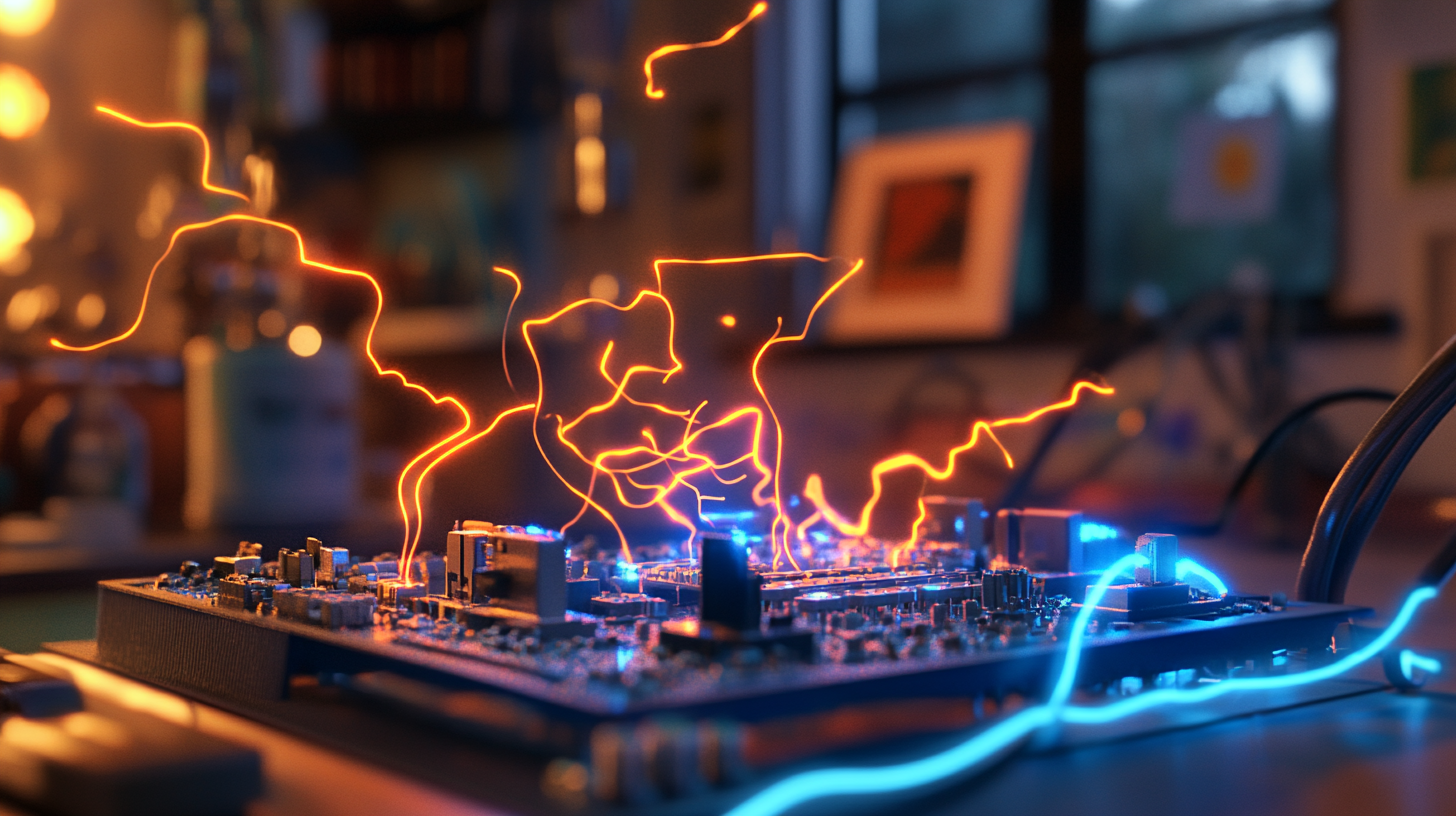
Understanding the Importance of Electrical Safety Testing in Modern Facilities
Electrical safety testing is a fundamental aspect of maintaining modern facilities, particularly as the reliance on electrical systems continues to grow. Understanding the importance of these tests cannot be overstated; they serve not only to prevent accidents but also to ensure compliance with industry regulations. For instance, compliance with regulations set forth by authorities like OSHA is critical for the safe operation of electrical equipment. Recent insights from industry experts emphasize the risks associated with neglected inspections, which can lead to serious safety hazards and costly liabilities for businesses. In light of technological advancements, new facilities such as the recently inaugurated NABL-accredited electrical safety test facility at IIT Kanpur are leading the charge in enhancing safety standards. These state-of-the-art facilities are specifically designed to conduct comprehensive electrical safety testing, including Electromagnetic Interference and Compatibility assessments. This advanced testing capability is vital in promoting research and development, ultimately leading to safer electrical products in various applications. Furthermore, as experts predict a more tech-driven society by 2025, the emphasis on electrical safety testing becomes even more pronounced. With increasing complexity in electrical systems, regular and thorough safety testing is crucial in mitigating new risks. Modern facilities must not only embrace innovative technologies but also prioritize safety measures that protect both personnel and equipment from electrical hazards.
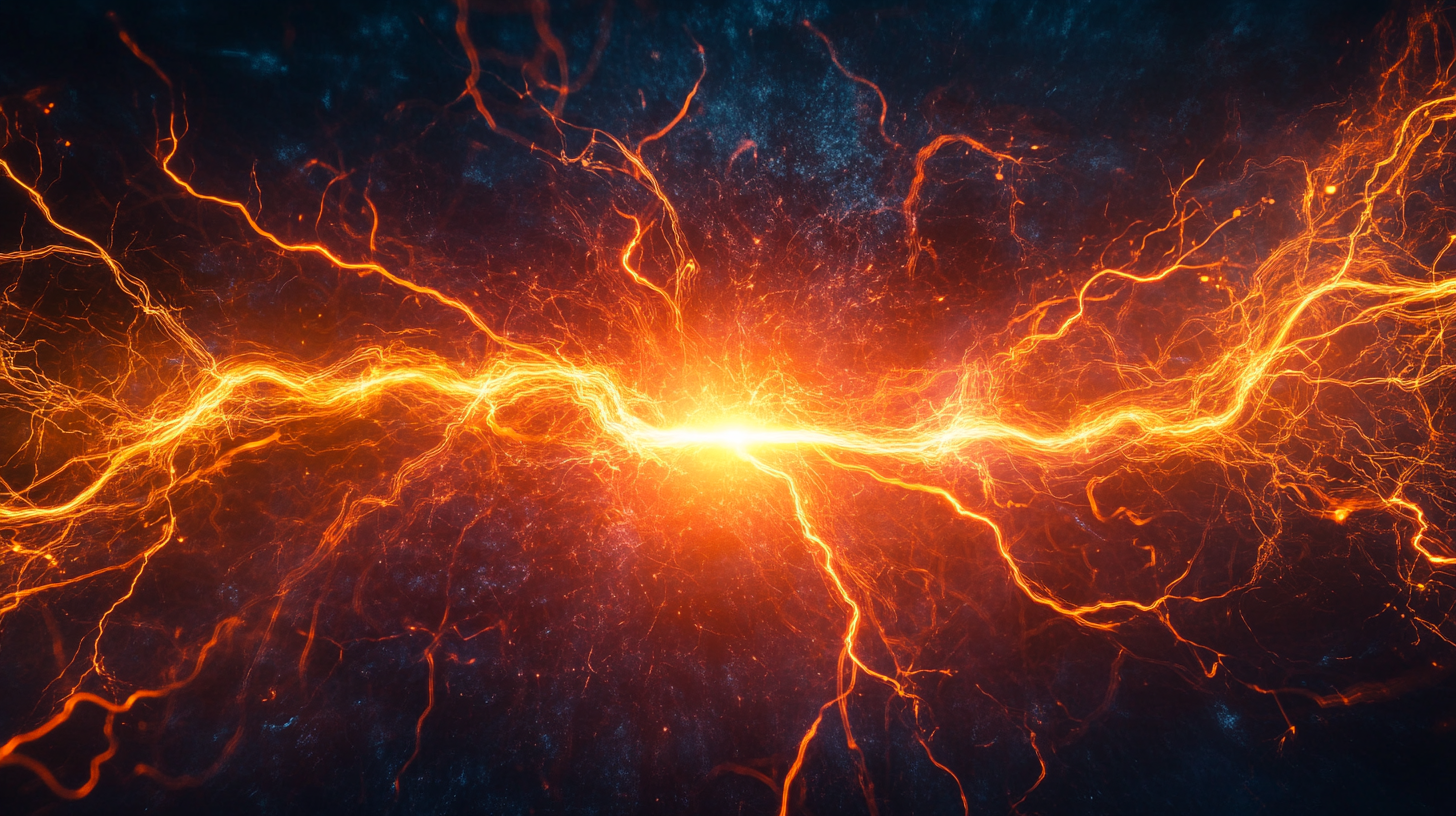
Key Techniques for Preparing Equipment and Environment for Electrical Testing
When conducting electrical safety testing, the preparation of both the equipment and the environment plays a pivotal role in ensuring accurate results and minimizing risks. First and foremost, it is crucial to inspect and service all electrical devices prior to testing. This includes checking that all connections are secure, there are no visible signs of damage, and that all components are operating as intended. Regular maintenance not only enhances the safety of the equipment but also contributes to obtaining precise readings during testing.
Equally important is the environmental setup where testing will occur. The area should be clean, dry, and well-lit to prevent any unsafe conditions from arising. Any unnecessary clutter should be removed, and all safety barriers should be in place. Additionally, ensuring that the area is well-ventilated is critical to dissipate any potential hazardous fumes or gases that might be emitted during testing. Implementing an organized workspace minimizes distractions and allows testers to focus on the task at hand, further enhancing safety protocols.
Lastly, proper use of personal protective equipment (PPE) cannot be overlooked. Each technician should don appropriate gear such as gloves, safety glasses, and insulating mats tailored to the nature of the electrical testing being performed. By prioritizing these preparations—both in equipment and environment—organizations can significantly elevate safety standards and ensure the successful execution of electrical safety tests.
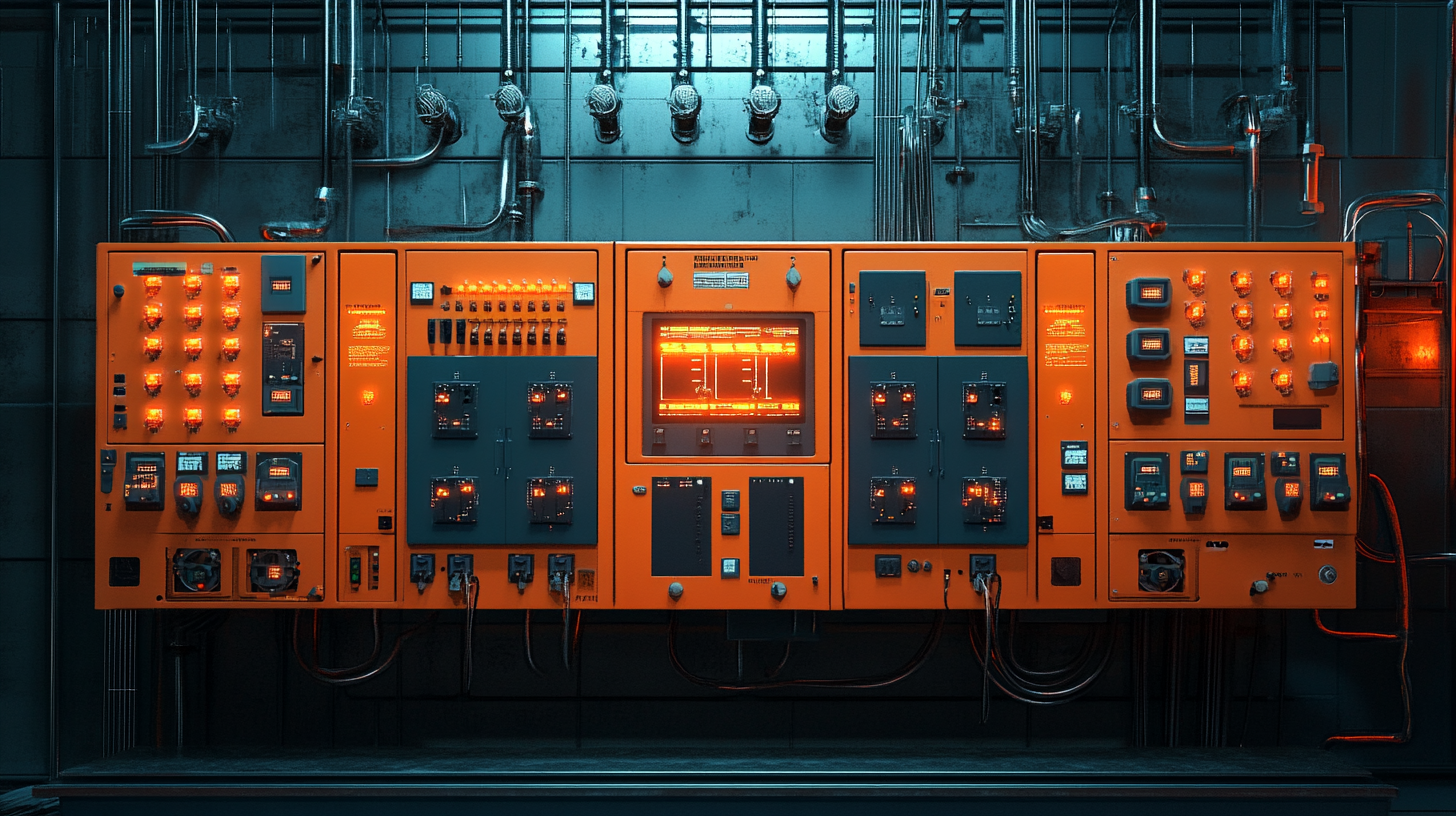
Common Risks During Electrical Testing and How to Mitigate Them
Electrical safety testing is crucial for maintaining safe operations in various industries. However, it comes with its own set of risks that can lead to severe consequences if not properly managed. According to the National Fire Protection Association (NFPA), electrical malfunctions accounted for approximately 13% of all reported fires in the United States in 2020. To mitigate these risks, it is essential to adopt best practices in the testing process.
One of the common risks during electrical testing is the exposure to live circuits. This can cause serious injuries or even fatalities. The Occupational Safety and Health Administration (OSHA) emphasizes the importance of de-energizing equipment before testing whenever possible. Utilizing lockout/tagout (LOTO) procedures can significantly reduce the risk of unexpected energization. Additionally, providing personal protective equipment (PPE), such as insulated gloves and face shields, can further safeguard testers from electrical hazards.
Another significant risk arises from equipment failure or improper testing procedures. A study published by the Institute of Electrical and Electronics Engineers (IEEE) found that improper use of testing equipment was responsible for approximately 30% of electrical testing accidents. To combat this, regular training and certification updates for technicians are essential. Implementing strict adherence to industry standards such as those outlined in the National Electrical Code (NEC) can greatly contribute to a safer testing environment and ensure the reliability of results.
Overall, understanding and addressing these common risks during electrical safety testing not only protects personnel but also enhances operational efficiency and compliance with safety regulations.
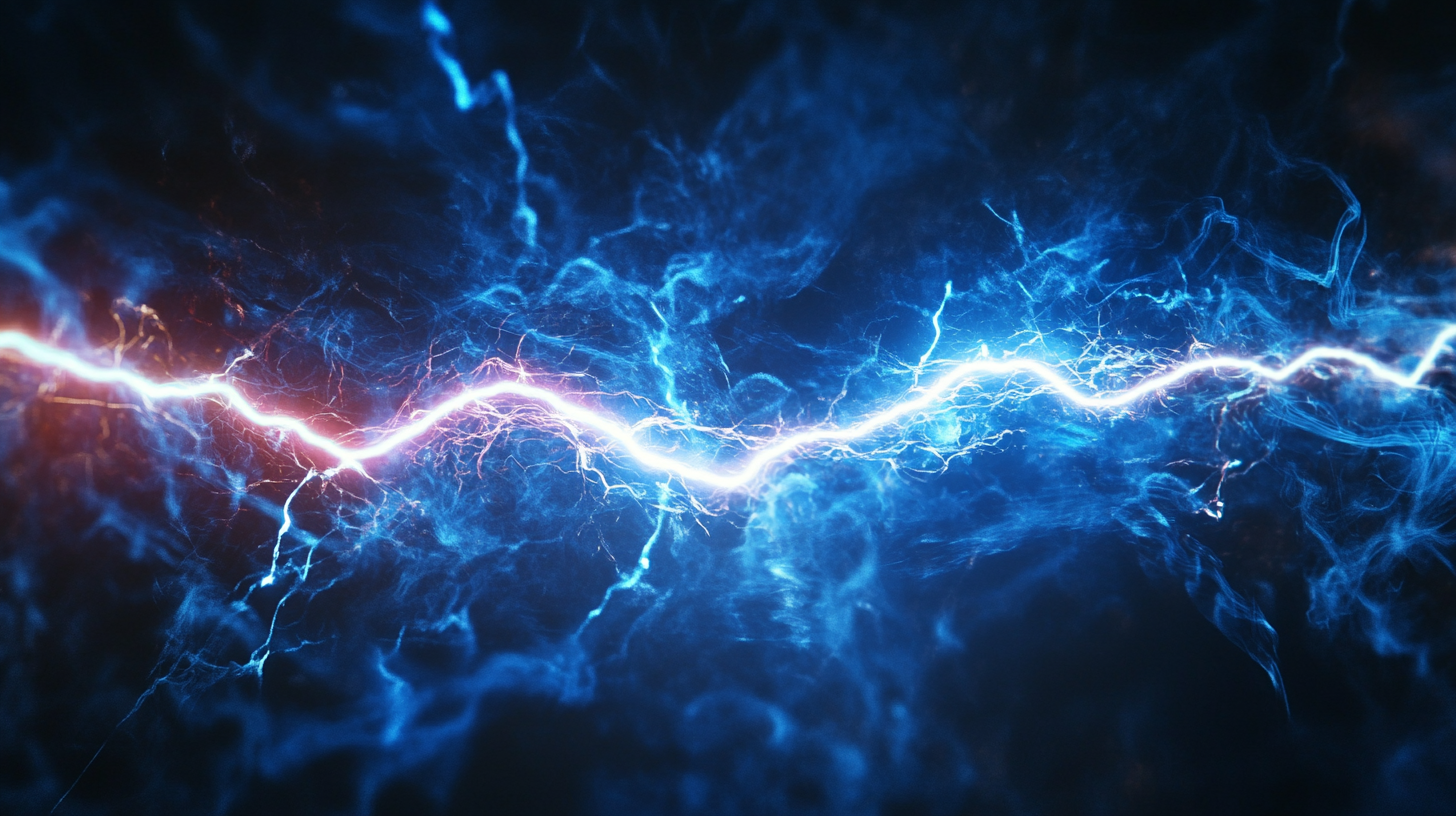
Best Practices for Documenting Electrical Safety Testing Results
When it comes to electrical safety testing, accurate documentation of results is crucial not only for compliance but also for enhancing the reliability of the equipment. According to a recent report by the National Fire Protection Association (NFPA), improper documentation contributes to nearly 30% of electrical-related incidents, highlighting the importance of thorough record-keeping. Implementing best practices for documenting testing results can significantly mitigate risks, ensuring that vital information is accessible and clear for future references.
One effective method is to standardize documentation processes across your organization. Utilizing templates that include key data points such as test dates, methodologies, and results can improve consistency. A study published in the Journal of Electrical Safety and Compliance found that organizations that maintained standardized documentation were 50% more likely to pass regulatory audits. Additionally, integrating digital tools for tracking and storing results can enhance data accuracy and accessibility, as papers can easily be lost or damaged.
Moreover, it’s essential to include detailed notes on any anomalies recorded during testing. This practice not only provides a clearer picture of the equipment's health but also offers insights into potential future issues. According to the International Electrotechnical Commission (IEC), facilities that engage in detailed annotated documentation report a decrease in failure rates by up to 40%. By prioritizing comprehensive and structured documentation methods, companies can bolster both compliance and safety within their electrical systems.
Ensuring Compliance with Standards and Regulations in Electrical Safety Testing
Ensuring compliance with standards and regulations in electrical safety testing is critical for any organization that designs or manufactures electrical equipment. According to a report by the International Electrotechnical Commission (IEC), approximately 70% of electrical accidents can be traced back to non-compliance with established safety standards. These statistics highlight the importance of rigorous electrical safety testing to prevent hazards associated with poorly designed or manufactured electrical devices.
One essential aspect of compliance is understanding the various standards that govern electrical safety, including IEC 60950 for information technology equipment and IEC 60601 for medical devices. These regulations provide comprehensive guidelines that manufacturers must follow to ensure the safety of their products. In 2022, over 95% of products that underwent third-party testing met these safety standards, underscoring the importance of proper testing protocols in achieving compliance.
Furthermore, keeping documentation up-to-date is crucial for demonstrating compliance with safety regulations. A survey from the National Fire Protection Association (NFPA) found that organizations with thorough documentation practices reduced the risk of electrical fires by 40%. This trend emphasizes the necessity of meticulous record-keeping in electrical safety testing, facilitating quicker audits and compliance verification with regulatory bodies. Therefore, organizations must prioritize these practices to ensure the reliability and safety of their electrical products.