- Home
- News
Navigating Industry Production Standards: Unveiling Common Issues in Electrical Safety Testing
In today's rapidly evolving technological landscape, the importance of Testing Electrical Safety cannot be overstated. According to the International Electrotechnical Commission (IEC), electrical accidents account for over 30% of workplace fatalities related to electrical hazards worldwide. In the quest for compliance with industrial production standards, manufacturers must navigate a myriad of challenges that can compromise both product integrity and consumer safety. Recent studies indicate that improper testing methods and lack of adherence to established guidelines lead to significant increases in product recalls, with the National Fire Protection Association (NFPA) reporting that non-compliance can cost companies millions in liabilities. Thus, understanding the common issues and best practices in electrical safety testing is not only crucial for safeguarding end-users but also essential for sustaining a manufacturer’s reputation in today’s competitive market.
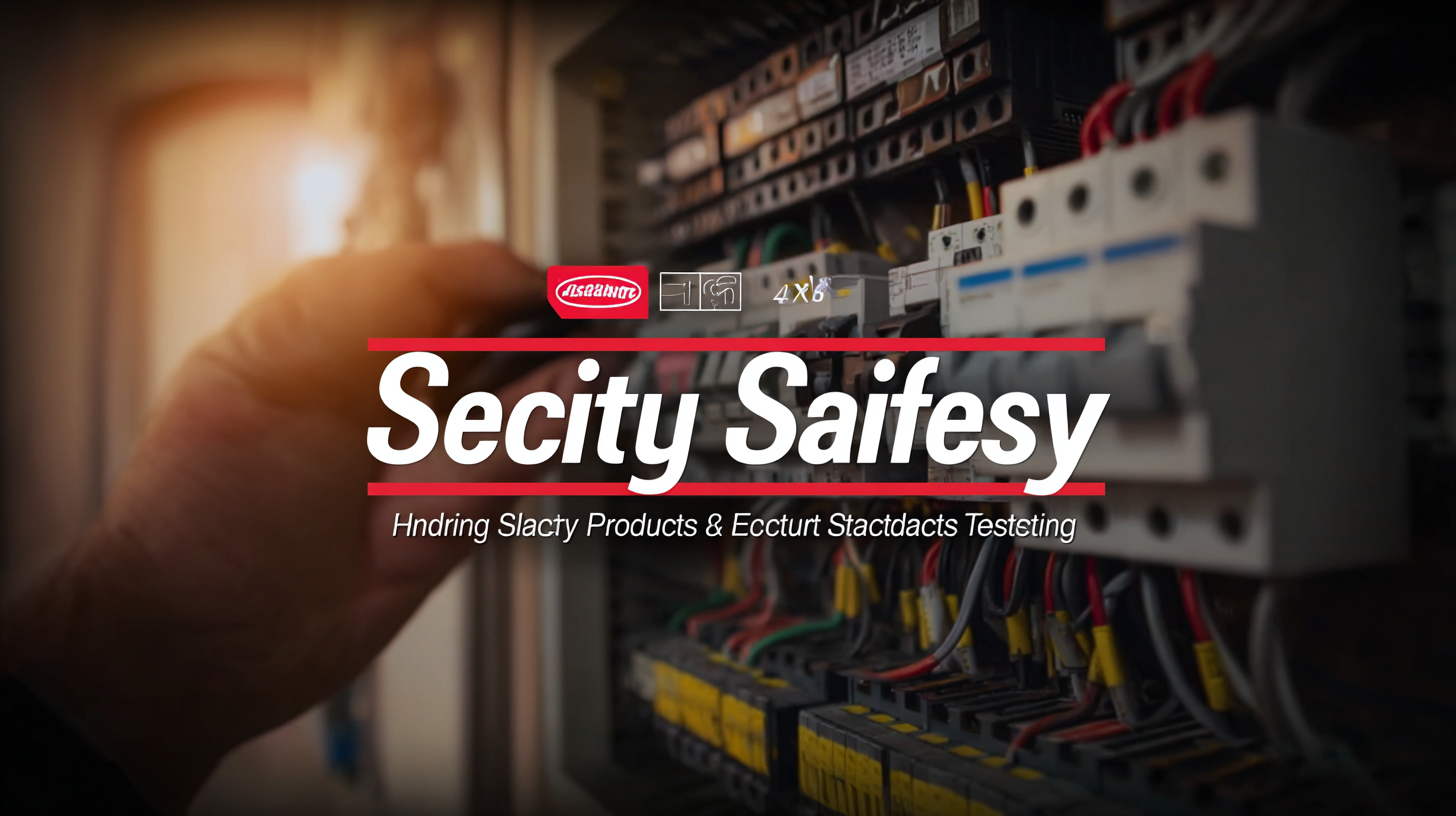
Understanding Electrical Safety Testing Standards
Electrical safety testing is crucial for ensuring that products meet the necessary industry standards before they reach consumers. Understanding these standards not only helps manufacturers comply with regulations but also protects end-users from potential hazards. The testing process often evaluates various parameters, including insulation resistance, dielectric strength, and earth continuity, among others. Familiarizing yourself with these key aspects can significantly enhance the safety and reliability of your products.
**Tip: Always keep updated with the latest standards and amendments in electrical safety testing. Industry standards can evolve, and staying informed helps businesses adapt quickly and maintain compliance.**
Common issues that arise during electrical safety testing include inadequate documentation or misinterpretations of testing procedures. Many manufacturers might overlook the importance of thorough documentation, which is essential for demonstrating compliance during audits. Also, engaging with certified testing laboratories can provide valuable insights and mitigate the risks associated with non-compliance.
**Tip: Collaborate with experts in electrical safety testing. Establishing relationships with certified professionals can streamline the testing process and help identify potential issues early in the product development phase.**
Navigating Industry Production Standards: Unveiling Common Issues in Electrical Safety Testing
Standard Type | Standard Number | Common Issues | Impact on Safety |
---|---|---|---|
IEC 60950 | EN 60950 | Insufficient thermal management | Risk of overheating and fire |
IEC 60335 | EN 60335 | Inadequate insulation | Electric shock hazards |
UL 60950 | CAN/CSA C22.2 | Failure to meet drop test requirements | Risk of mechanical failure |
IEC 61558 | EN 61558 | Heat dissipation issues | Potential burn hazards |
IEC 61000 | EN 61000 | Inadequate electromagnetic compatibility | Operational failures and data loss |
Identifying Common Pitfalls in Industry Practices
In the landscape of electrical safety testing, identifying common pitfalls in industry practices is crucial to ensure compliance and safety. One prevalent issue is the inadequate understanding of production standards, which can lead to testing failures. Companies often assume they are compliant without fully grasping the nuances of the regulations, resulting in costly recalls and reputational damage.
**Tips:** To navigate these challenges, organizations should implement a thorough training program that covers the essentials of electrical safety standards. Regularly updating this training ensures that all employees are informed about the latest regulations and best practices, reducing the likelihood of oversights.
Another common pitfall is the lack of effective communication between different departments involved in the testing phase. When engineering, manufacturing, and quality assurance teams do not collaborate, discrepancies can arise, leading to ineffective testing protocols.
**Tips:** Establishing cross-departmental meetings can facilitate a more cohesive approach. Additionally, utilizing project management tools to share information and updates can enhance transparency, ensuring everyone is on the same page throughout the testing process. Emphasizing these practices not only promotes safety but also drives efficiency in achieving compliance.
Navigating Industry Production Standards: Electrical Safety Testing Issues
Creating an Effective Electrical Safety Testing Checklist
Creating a comprehensive electrical safety testing checklist is essential for ensuring compliance with industry production standards. An effective checklist serves as a vital tool for manufacturers and engineers alike, outlining specific tests and criteria that electrical products must meet to be deemed safe for consumer use. To start, the checklist should include mandatory tests like insulation resistance tests, dielectric withstand tests, and earth continuity tests, each designed to identify potential hazards that could lead to electrical shock or fire hazards.
Furthermore, it’s important to incorporate routine inspections and maintenance checks into the checklist. These can include visual inspections for damaged components, functional tests to ensure all parts are operating as intended, and thermal imaging assessments to detect overheating issues. By using a structured checklist during each testing phase, companies can systematically identify common issues and address them proactively, ultimately enhancing product safety and reliability in the market. This not only protects end-users but also helps manufacturers avoid costly recalls and legal repercussions associated with non-compliance.
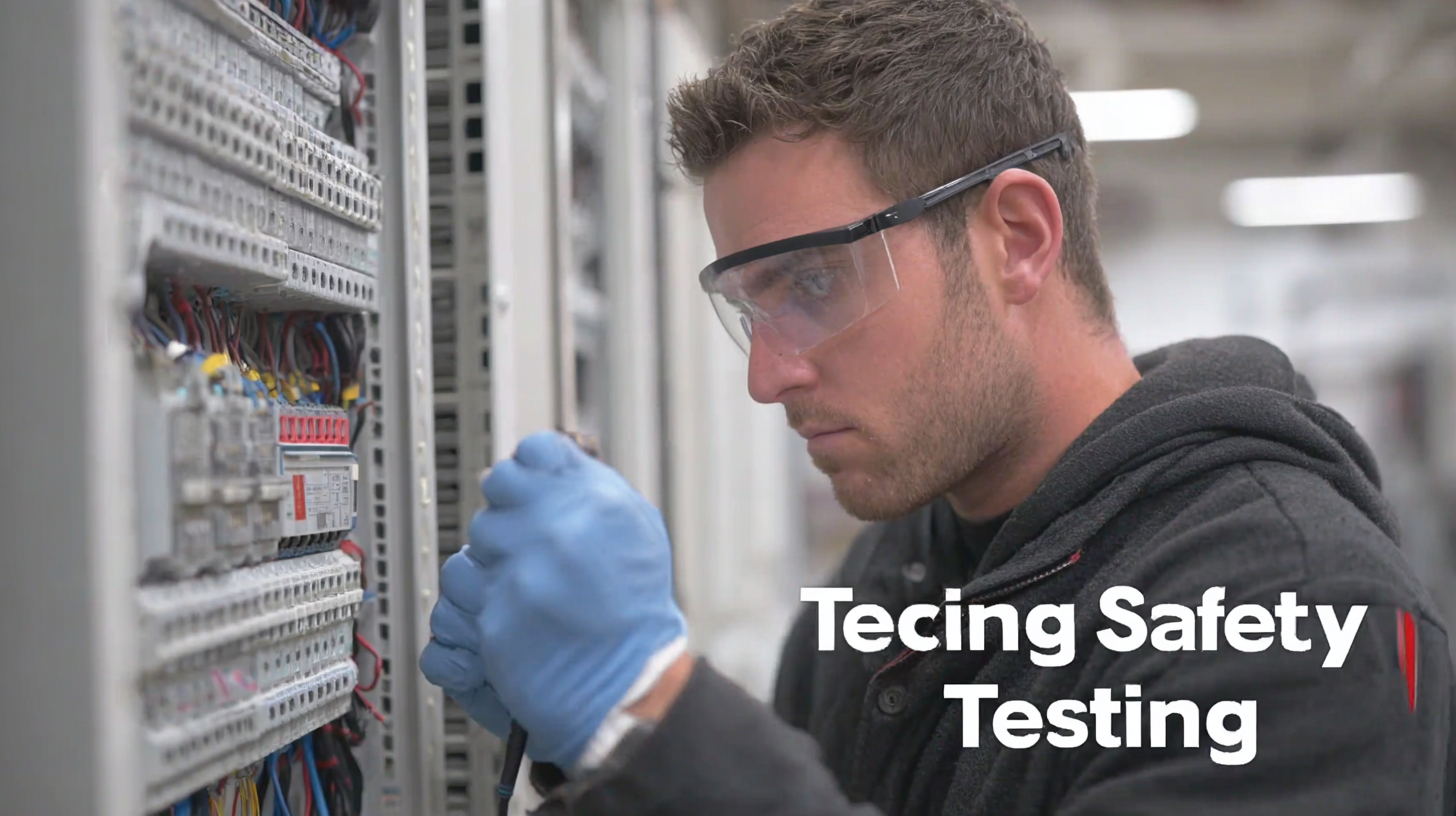
Implementing Solutions to Improve Testing Compliance
In the realm of electrical safety testing, compliance with industry production standards is crucial for manufacturers aiming to ensure safe and reliable products. However, many companies encounter common issues that hinder effective testing processes. One prominent challenge is the lack of standardized protocols across different markets, which can lead to confusion and non-compliance. By implementing clear guidelines and harmonizing testing methods globally, companies can mitigate these risks and enhance their compliance rates.
Moreover, investing in advanced testing technologies can significantly improve the accuracy and efficiency of safety assessments. Automated testing solutions not only streamline the process but also provide real-time data analytics that help identify potential safety hazards early on. Additionally, training personnel on the latest industry standards and testing procedures fosters a culture of safety and quality within the organization. By prioritizing these solutions, manufacturers can navigate the complexities of electrical safety testing and ensure their products meet the stringent requirements necessary for market acceptance.
Staying Updated on Evolving Industry Standards and Regulations
In the rapidly evolving landscape of electrical safety testing, staying abreast of new industry standards and regulations is crucial for manufacturers and safety professionals. As technology advances, so do the expectations set forth by regulatory bodies, which can often lead to confusion and challenges for those in the electrical sector. Regular updates from organizations such as the International Electrotechnical Commission (IEC) and Underwriters Laboratories (UL) are essential to ensure compliance and safety in product development.
Moreover, understanding the implications of these evolving standards plays a key role in mitigating risks associated with electrical products. Manufacturers must not only adhere to existing regulations but also anticipate future changes that could impact their operations. This proactive approach includes investing in training and resources to familiarize teams with both compliance obligations and best practices in electrical safety. By prioritizing continuous education, businesses can effectively minimize safety hazards while maintaining a competitive edge in the industry.