- Home
- News
What Are the Key Standards for Testing Wires For Power in Global Supply Chains?
In an increasingly interconnected global marketplace, the integrity of electrical components, particularly Testing Wires for Power, is of paramount importance. According to a recent report by the International Electrotechnical Commission (IEC), the demand for reliable power transmission has surged by 25% over the last decade, driven by advances in renewable energy technologies and the expansion of electric vehicles. This rising demand underscores the need for stringent testing standards that ensure safety, efficiency, and longevity in wire products utilized across diverse applications.
Global supply chains are highly complex, often involving multiple stakeholders and varied regulatory environments. A report from the Global Supply Chain Council highlighted that up to 90% of electrical failures can be traced back to substandard wiring, emphasizing the critical role of standardized testing protocols. Establishing robust testing standards for wires not only mitigates risks associated with electrical failures but also enhances product quality and consumer confidence. This blog will explore the key standards currently shaping the landscape of Testing Wires for Power, offering insights into best practices and compliance measures necessary for success in today's global supply chains.
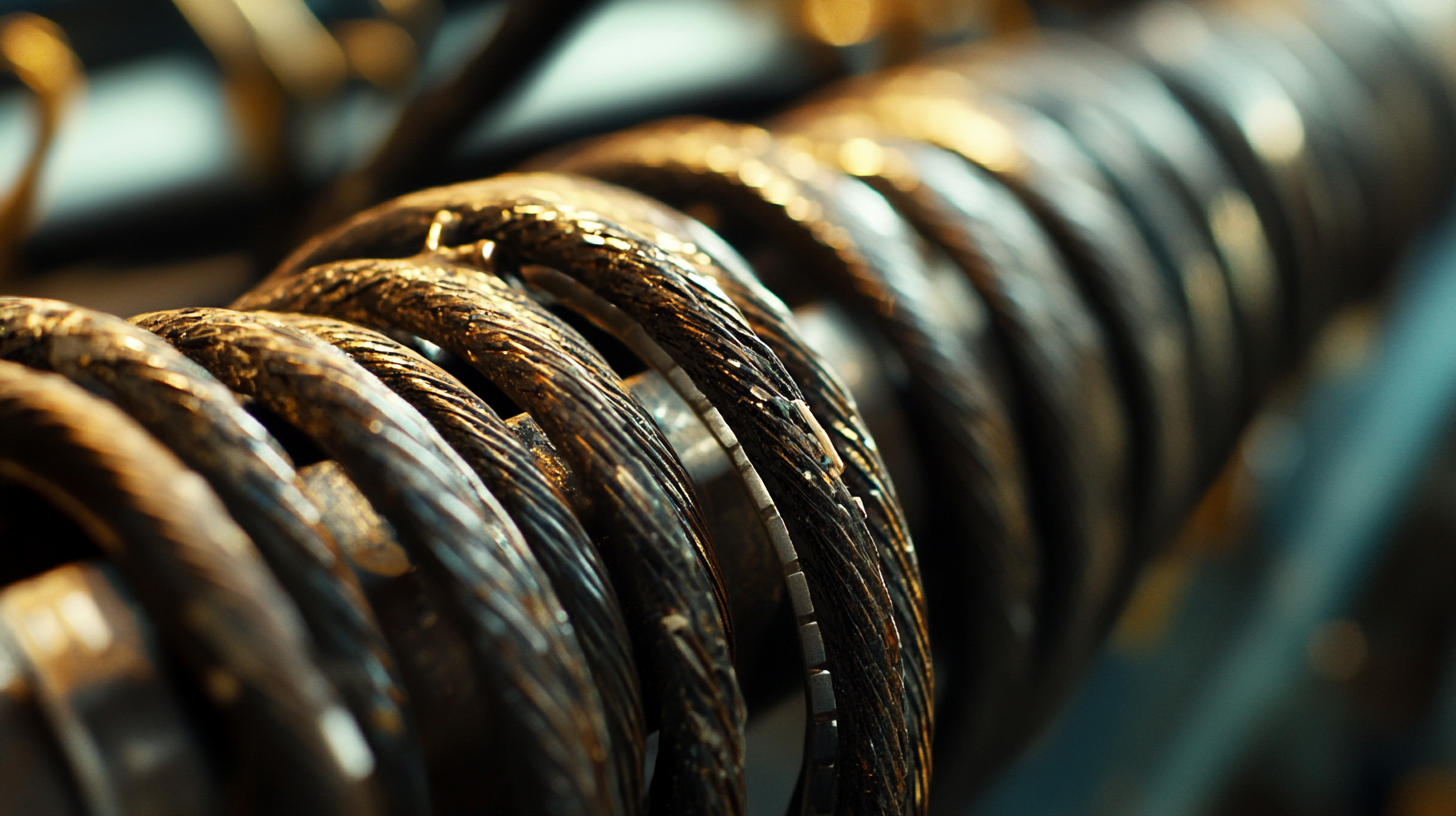
Key Regulatory Standards for Power Wire Testing in Global Markets
The global market for power wire testing is becoming increasingly complex as regulations evolve to ensure safety and reliability in supply chains. Key regulatory standards are vital for testing wires in power applications, especially as industries face growing scrutiny regarding quality assurance and environmental impact. Adherence to these standards not only promotes consumer safety but also enhances the credibility of manufacturers in global markets. Organizations must navigate a multitude of testing requirements set by regulatory bodies across different regions. This includes compliance with international standards that govern electrical safety, performance, and environmental protection. The most recognized standards provide benchmarks for evaluating the durability, conductivity, and thermal characteristics of power wires, which are crucial for ensuring long-term performance in various applications, from industrial uses to consumer electronics. Moreover, as sectors like electric vehicles gain momentum, the importance of rigorous wire testing becomes even more pronounced. The electric vehicle battery testing market, projected to see significant growth in the coming years, underscores the need for reliable power sources. Adherence to key standards not only mitigates risk but also supports innovation by encouraging manufacturers to adopt advanced testing methodologies that enhance product integrity and market competitiveness.
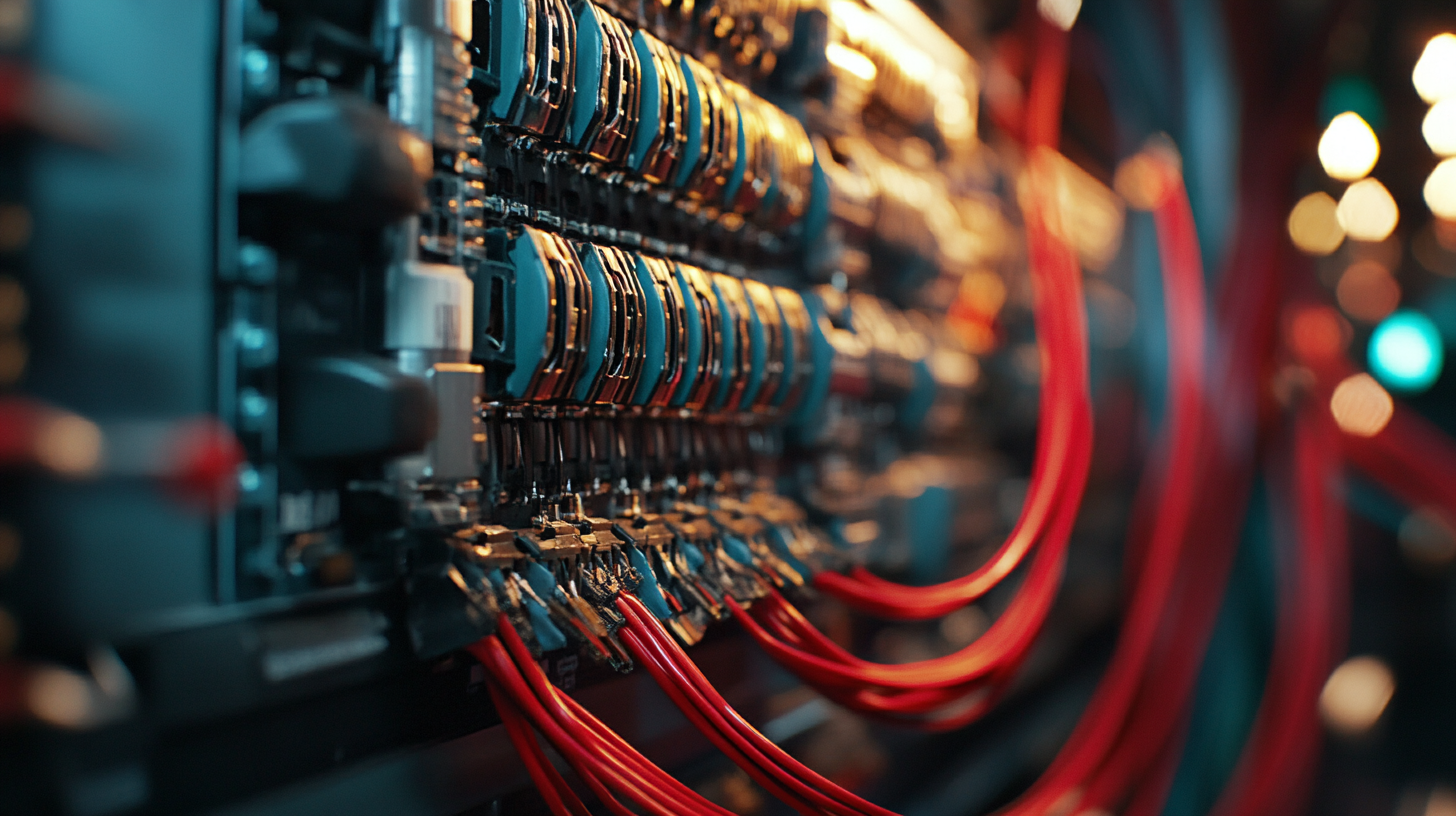
Essential Testing Methods for Ensuring Wire Safety and Performance
Ensuring the safety and performance of wires used in power applications is critical in global supply chains. The complex nature of modern manufacturing requires adherence to stringent testing methods. Among these, the International Electrotechnical Commission (IEC) standards play a vital role. According to a report by ResearchAndMarkets, the global electrical testing services market is projected to reach $37 billion by 2025, reflecting the growing emphasis on compliance and safety in wire manufacturing.
One essential testing method is the insulation resistance test, which evaluates the integrity of wire insulation. This process helps in identifying potential failures that could lead to short circuits or electrical fires. The IEEE Standards Association outlines that a minimum insulation resistance of 1 MΩ per kV operating voltage is typically recommended. Conducting these tests ensures that the wires can withstand environmental stresses, such as humidity and temperature fluctuations, which are crucial for maintaining performance in various applications.
Additionally, conductivity tests are vital for determining the quality of the wire. The American Society for Testing and Materials (ASTM) provides specifications that highlight acceptable conductivity levels for different materials. For instance, copper wires should exhibit conductivity levels no less than 100% IACS (International Annealed Copper Standard). With the rise of stringent regulations from agencies like the Occupational Safety and Health Administration (OSHA), it is imperative for manufacturers to not only conduct these tests but also to document compliance meticulously to avoid costly recalls or penalties.
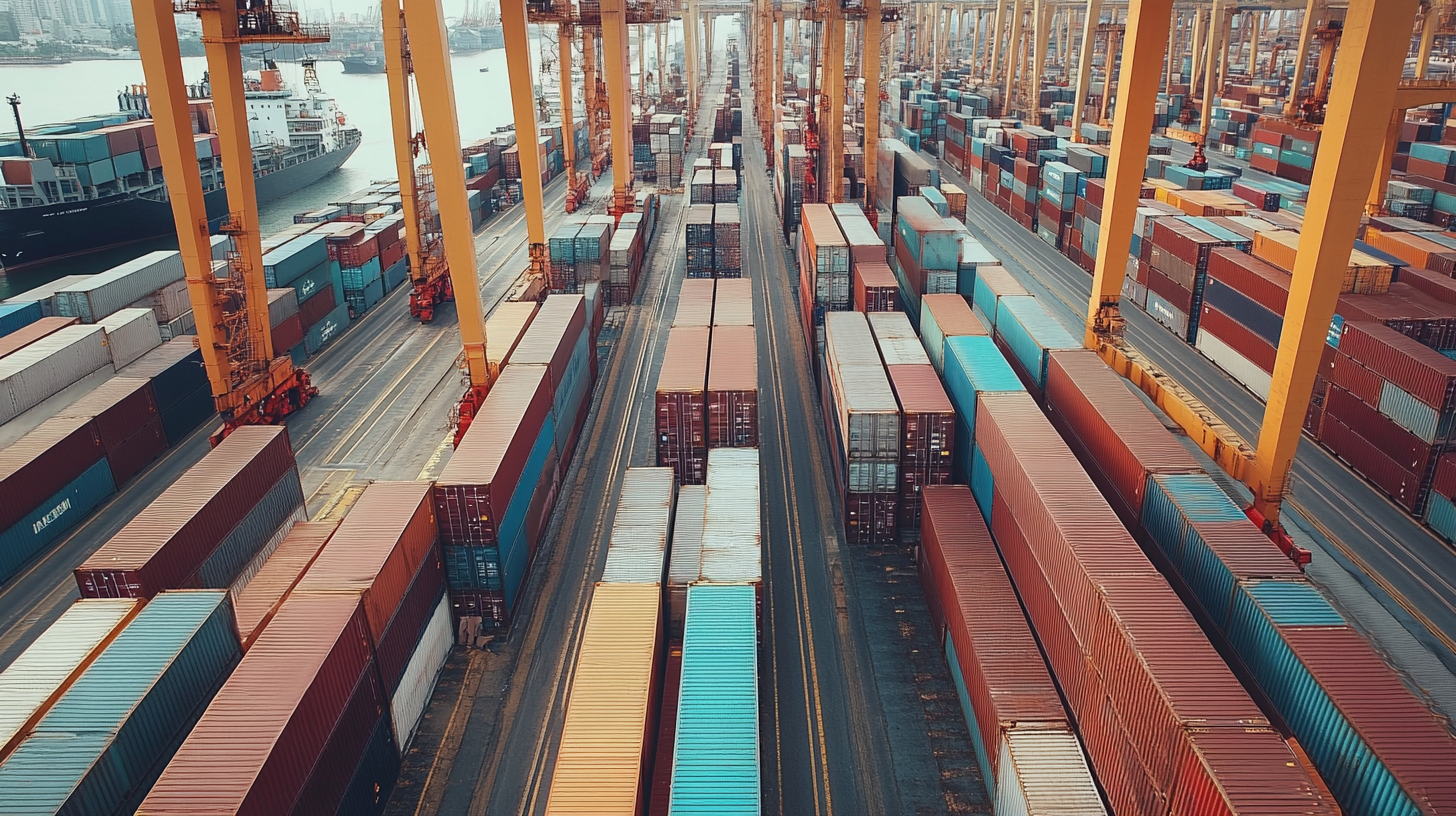
Impact of Compliance on Supply Chain Efficiency and Reliability
In today's global supply chains, the compliance of wires used for power transmission is crucial for maintaining efficiency and reliability. Adhering to established standards ensures that products function correctly and meet safety regulations, which can significantly reduce the risk of failures. Companies that fail to comply with these standards not only expose themselves to potential losses from defective products but also face reputational damage that can impact their market position.
The impact of compliance on supply chain efficiency cannot be overstated. When manufacturers utilize wires that meet international standards, they enhance their ability to operate seamlessly across borders. This leads to reduced delays in production caused by quality checks and rework, allowing businesses to deliver products to market more swiftly. Furthermore, compliant products facilitate smoother interactions with partners and suppliers, fostering a more agile supply chain that can adapt to changes in demand with less friction.
Reliability is another critical aspect affected by compliance. Wires that adhere to stringent testing standards are less likely to fail under various conditions, such as temperature fluctuations and mechanical stress. This reliability translates into greater operational stability for companies, ultimately leading to higher customer satisfaction and loyalty. In an increasingly competitive landscape, maintaining compliance is not just a regulatory concern but a strategic advantage that can enhance the overall resilience of a company's supply chain.
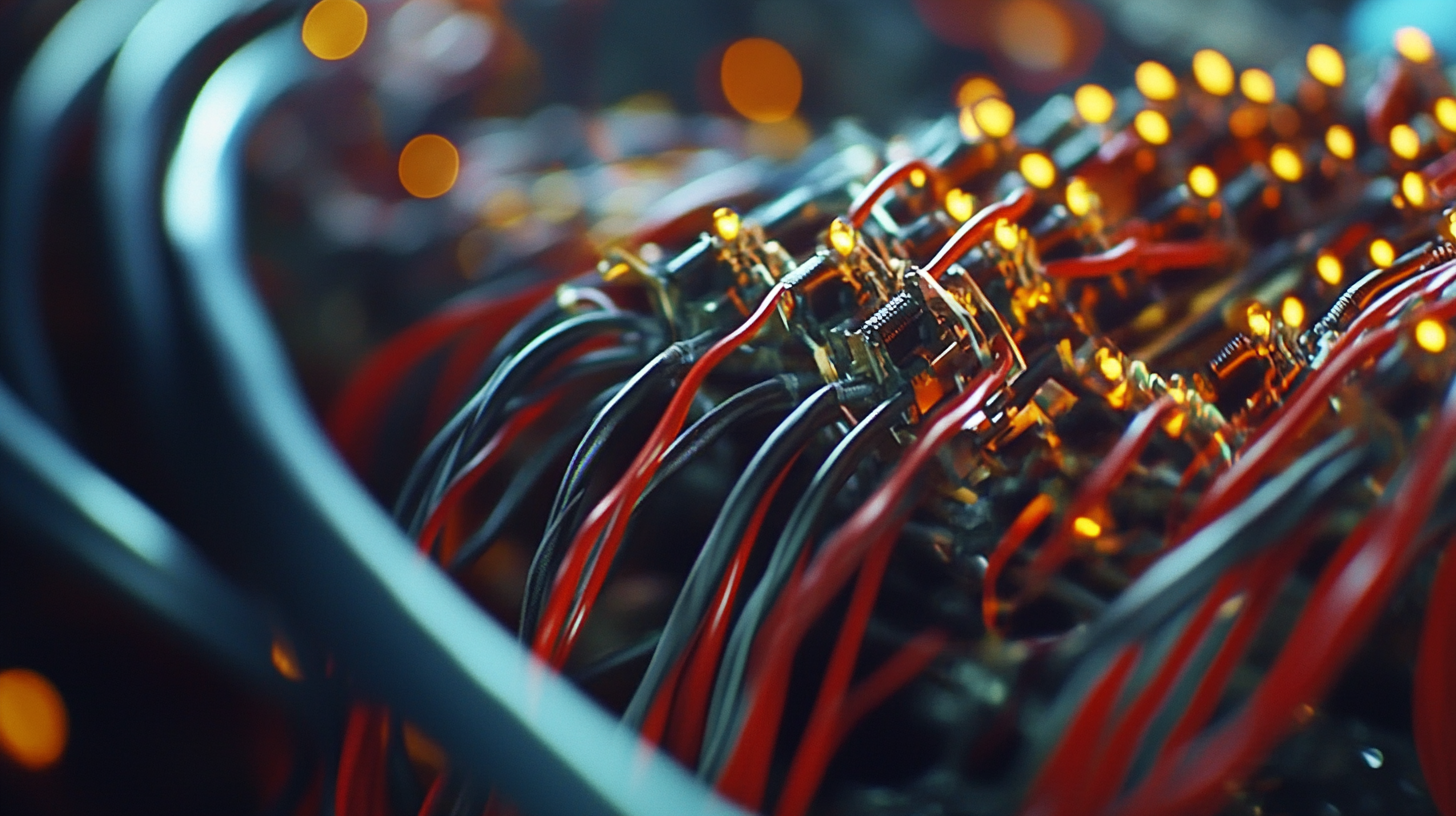
Emerging Technologies and Innovations in Wire Testing Standards
Emerging technologies have revolutionized the landscape of wire testing standards in global supply chains, ensuring enhanced safety and reliability for energy transmission. As industries increasingly rely on advanced materials and innovative designs, traditional testing methods often fall short in addressing the complexities posed by modern wire applications. New testing standards are being developed to accommodate the unique electrical, thermal, and mechanical properties of these materials, thereby streamlining evaluation processes and improving compliance across international borders.
Among the notable innovations is the integration of automation and smart technologies in wire testing. Automation not only speeds up the testing process but also enhances precision, minimizing human error in measurement and evaluation. Additionally, the incorporation of data analytics and artificial intelligence allows for real-time monitoring and assessment, enabling manufacturers to quickly identify potential failures and rectify them proactively. This shift toward data-driven methodologies ensures a higher level of quality assurance, aligning with the rigorous demands of global supply chains.
Moreover, the shift towards sustainability in manufacturing practices has prompted the development of new wire testing standards that emphasize eco-friendliness. Tests now consider the environmental impact of materials and their lifecycle, pushing the industry towards greener alternatives. These evolving standards reflect broader trends in technology and environmental awareness, ultimately fostering a more resilient and responsible framework for wire testing, critical for meeting the growing demands of an interconnected world.
Best Practices for Manufacturers to Meet Global Wire Testing Standards
In the complex landscape of global supply chains, adherence to key standards for testing wires for power is critical for manufacturers. These standards not only ensure safety and reliability but also enhance the competitiveness of products in the marketplace. To align with these global wire testing standards, manufacturers must adopt best practices that encompass rigorous testing protocols, certification processes, and continual education.
One crucial practice is the implementation of standardized testing methods such as IEC 60227 and UL 83, which provide consistent guidelines for evaluating wire performance under various conditions. Manufacturers should invest in advanced testing technologies that simulate real-world environments and stress conditions. Regular audits and compliance checks further ensure that these testing methods are strictly followed, identifying potential non-compliance issues before they affect product quality.
Additionally, fostering a culture of safety and quality within the organization encourages employees to prioritize compliance with testing standards. Training programs should be established to keep staff updated on new regulations and technological advancements. Collaboration with industry experts and participation in global forums can also provide valuable insights into evolving standards and best practices. By embedding these strategies into their operations, manufacturers can not only meet but exceed global wire testing standards, thereby boosting their reputation and reliability in the supply chain.