- Home
- News
Electrical Check Standards: Unveiling Global Compliance Challenges in Manufacturing
Maximization of the benefits of technology in the manufacturing process not only leads to safety and compliance but also ensures that the productive industry stands high. Electrical check standards safeguard manufacturing environments through protection of equipment, safety of personnel, and safety to end users. As more manufacturers are using more sophisticated systems, electrical checks become more complicated, yet it will be a global multifaceted challenge.
Electrical check standards are set globally; however, the compliance becomes tricky. Different regions follow through and adhere to quite different regulations, thus making a patchwork of requirements to be crossed by manufacturers. This inconsistent pattern complicates not only the compliance efforts but also raises alarms on the quality-reliability concern of manufactured products in international commercial markets. The more we delve into the detail of these electrical check standards, the clearer it becomes that those challenges in compliance should be taken care of to provide a unified global manufacturing landscape.
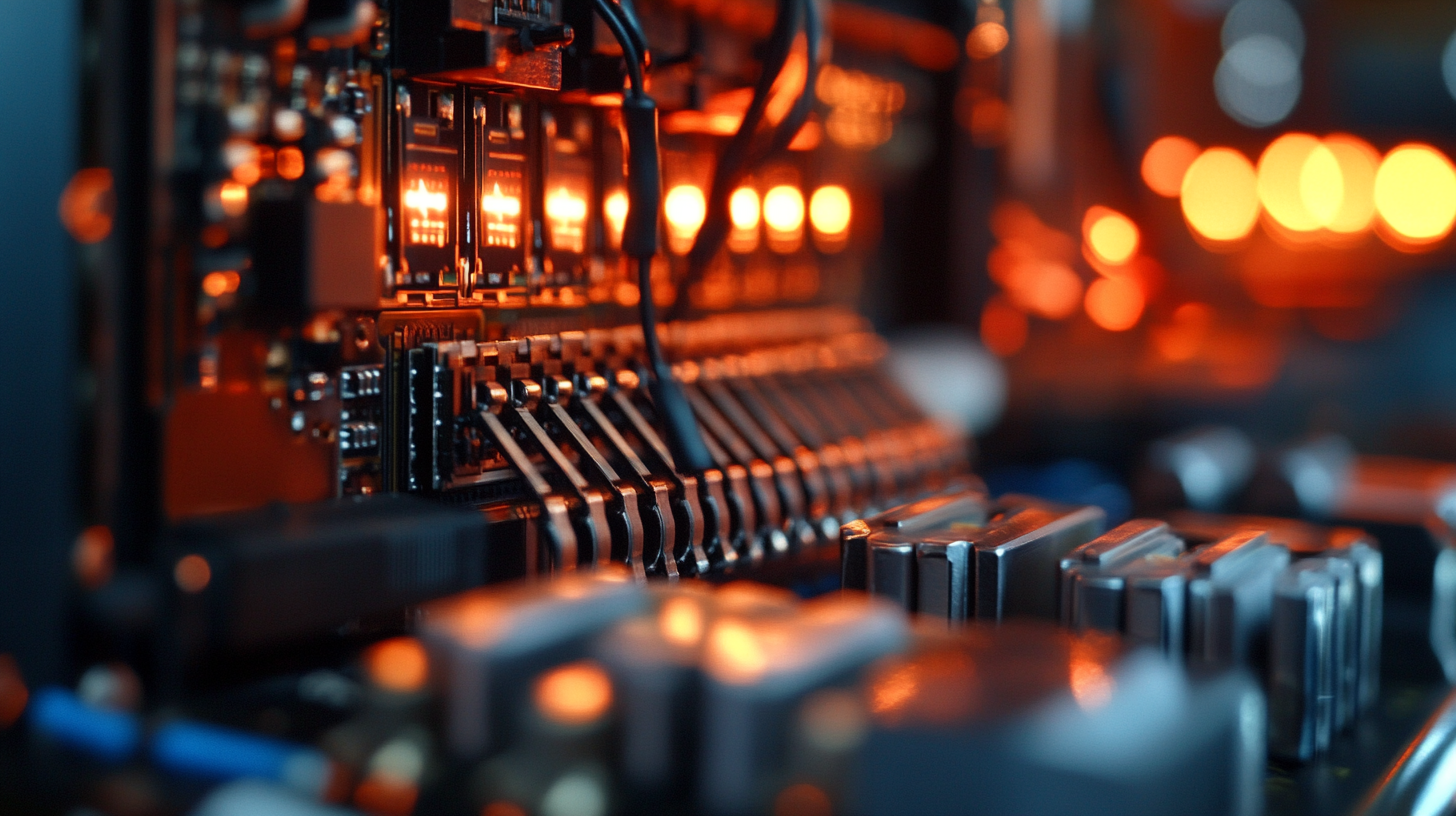
Emerging Electrical Check Standards in Global Manufacturing
Emerging electrical check standards evolve quickly today, and the changing global landscape makes them essential for integrated product safety and reliability. In addition, as technology advances, much pressure is upon manufacturers to adapt their products for international legislation evoking electrical testing and compliance. These standards are nowhere the same but differ significantly from region to region because of variations in safety norms, consumer expectations, and industry practices. An understanding of these standards will be helpful for those manufacturers who want to extend their market and thus ensure that their products are accepted by the local market. Most stakeholders now put onto the development of these standards one of their trends towards adopting eco-sustainable practices as an emerging commitment, forcing manufacturers to consider the performance, safety, and environmental impacts of electrical. Their actuator guidance gave rise to the means for testing that would assess energy efficiency and nontoxic materials within such. Therefore, manufacturers need to remain ahead by adopting sustainable practices in compliance strategies since this enhances brand reputation in line with global sustainability goals. Digitalization and automation are yet adding to the new dimensions of compliance in manufacturing. Such smart technologies enable near real-time monitoring of the electrical system, translating into more effective quality assurance processes. To avoid any unpleasant surprises, manufacturers use data analytics to head off possible compliance problems before they occur, literally at the speed of light. Sure, these technologies will continue to proliferate, so electrical check standards will likely become more streamlined, but with sufficient requirements to adapt quickly to really maintain compliance in a competitive global marketplace.
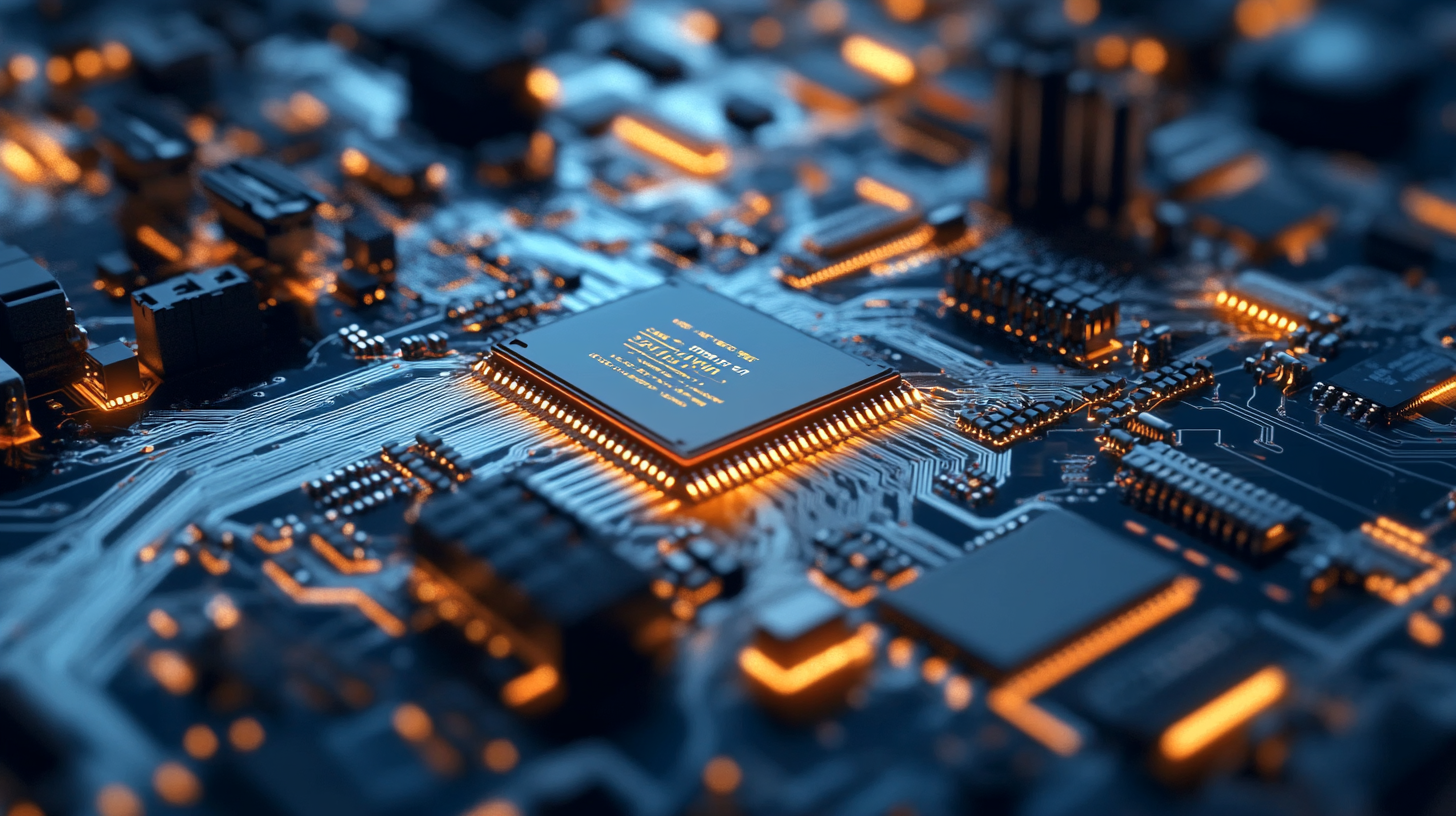
Key Compliance Challenges Faced by Manufacturers Worldwide
Adherence to electrical check standards is critical in today's world of global manufacturing. Compliance problems facing manufacturers are manifold; however, these are often region-specific and industry-specific. The problems get bigger with other RCCs, as regulators' requirements truly differ across different countries, creating an environment of almost impossible international compliance. Some regions emphasize safety standards, while others take a different perspective and concentrate on environmental impact. This piecemeal approach creates operational inefficiencies for manufacturers.
In a way, rapid advances in technology bring more headaches to compliance. When new electrical products are about to be launched in the market, it is common for the standards to be changed. This required the manufacturer to keep track of the changing standards, failing to do so would put the introduction on hold, thus delaying product launches and incurring hefty penalties should the product be found to have not satisfied the amended requirements. Coupled with the digitization of the manufacturing process come cyber security concerns, which must also be met with electrical compliance standards; thus multiply these already-complex regulations.
Manufacturers also face the challenge of ensuring compliance along their supply chains. With components procured globally, it is possible that the manufacturer is inadvertently violating compliance protocols because of a supplier's ignorance or lack of awareness concerning particular regulations. This defines the need for very strong compliance management systems with visibility and control over the entire supply chain. Simply put, to survive through these challenges, manufacturers ought to adopt a proactive compliance strategy that includes continuous learning flexibility and communication among all key stakeholders.
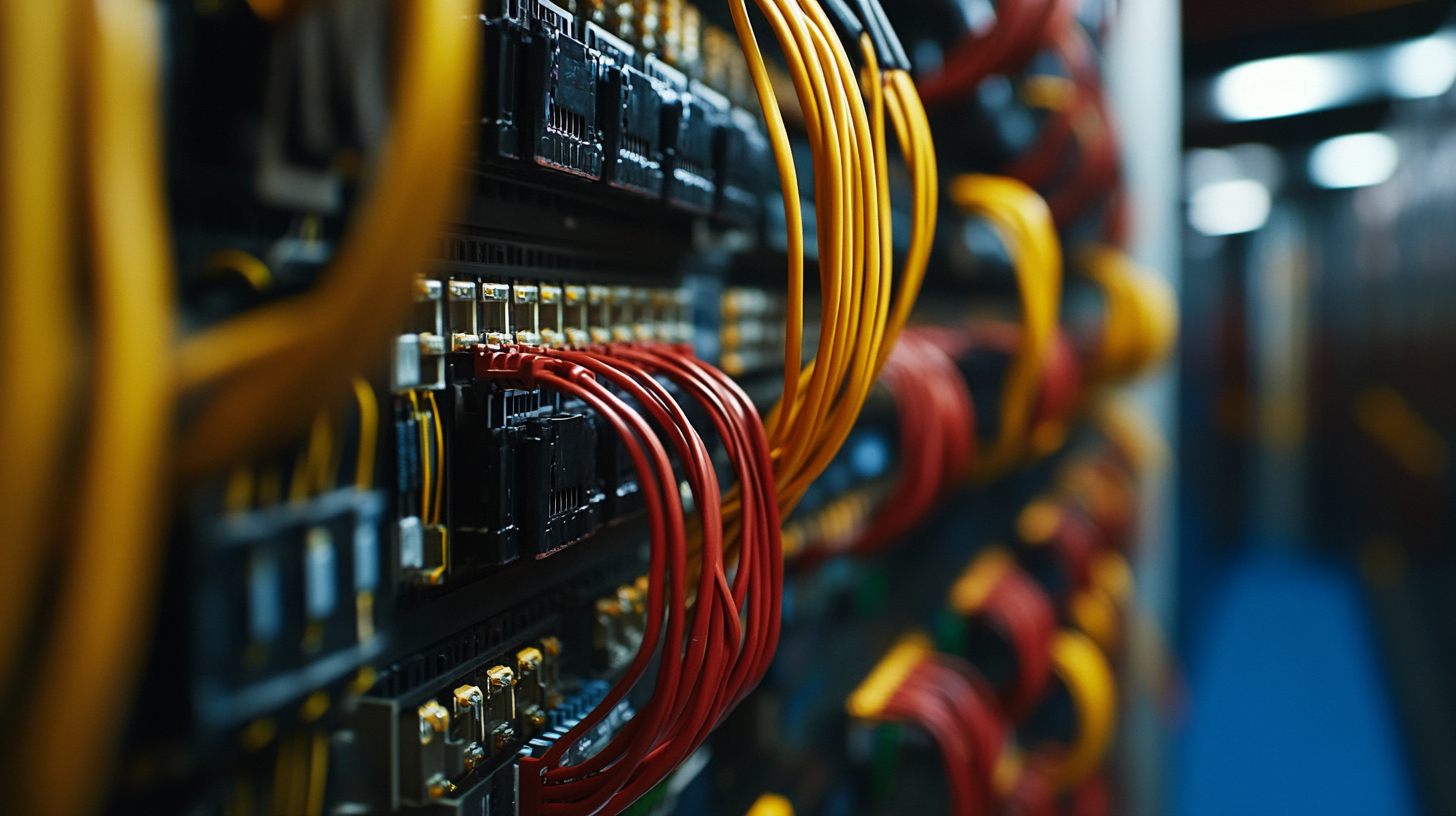
Impact of Regulatory Differences on Production and Financial Outcomes
This interplay between global manufacturing and diverse regulatory environments cannot allow one to underestimate the importance of the impact these differences have on producing and financial results. Many studies confirm that compliance with electrical-check standards affects operational efficiency and profitability. For instance, the International Electrotechnical Commission (IEC) asserts that manufacturers following stringent safety standards may cut electrical failures by 36%. Reduced risks act as a leg to stand on for better reliability with their product offerings into firm positioning.
The detailing of regulatory requirements often differ from one region to another. According to a recent study by the Global Compliance Group, companies operating among multiple jurisdictions see increased costs and complexities for about 47% of manufacturers who stated compliance challenges impact their overall production timelines. All those inconsistencies could lead to delays in launching products and increased operational costs which will hit financial performance.
With Chinese companies going global, the understanding of these regulatory relationships is central. The companies are required to adjust compliance toward local standards, which could entail an extensive investment in training and resources. Such adjustments are very important since studies indicate that companies adhering to local regulations could be as much as 25% more operationally efficient than companies that do not pay attention to such compliance; thus, regulatory adherence becomes a strategic lever for maximizing production capabilities and financial returns.
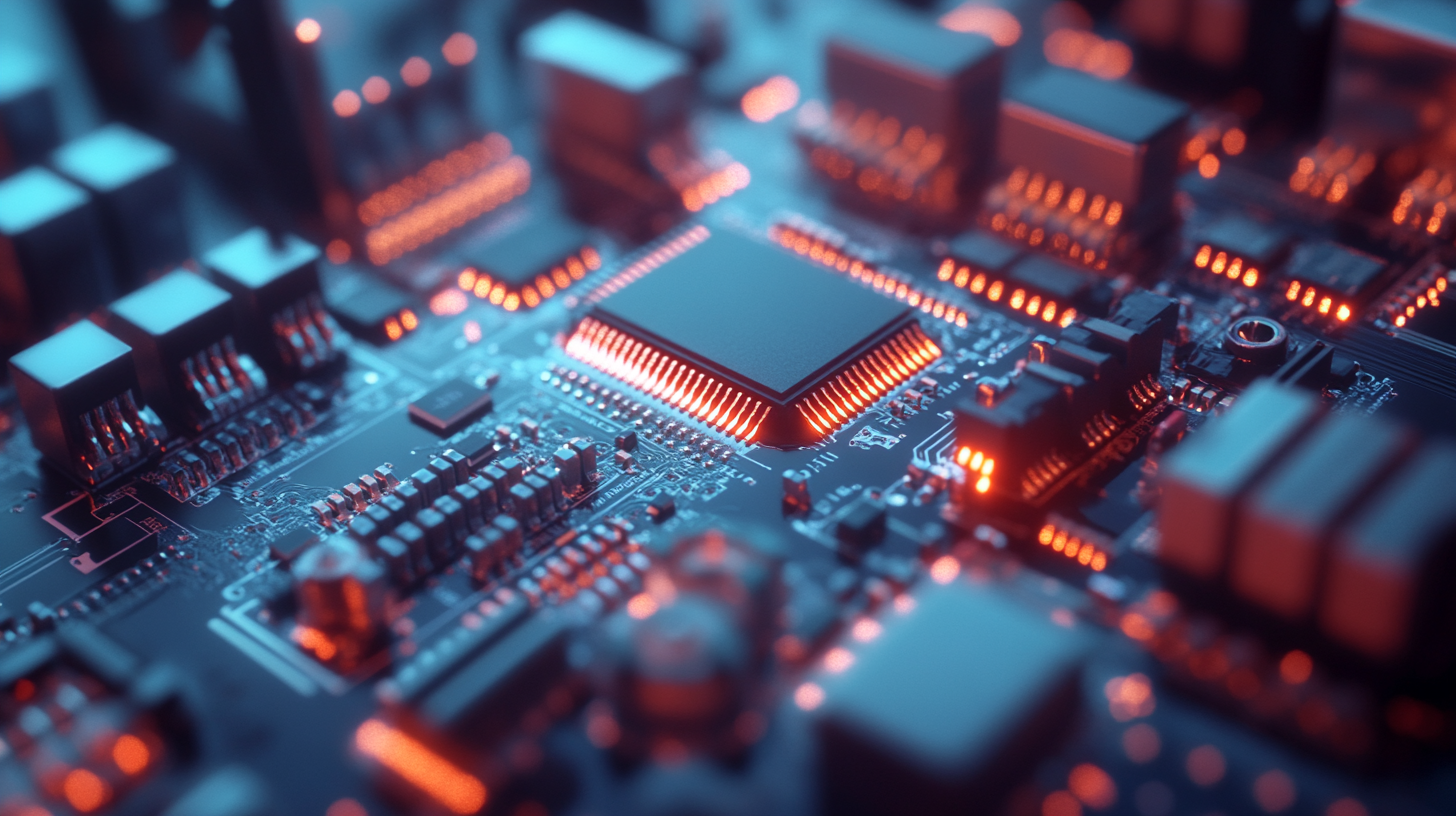
Strategies for Navigating International Electrical Compliance Requirements
International electrical compliance requirements serve as a potential minefield for manufacturers seeking to enter global markets. Product compliance-related issues tend to affect as much as 70% of electrical products, according to the International Electrotechnical Commission (IEC). Those very same compliance issues can keep a product from getting launched on time. Compliance requirements may differ from region to region, such as the European Union's Low Voltage Directive (LVD) and the United States' National Electrical Code (NEC). Therefore, it is important that companies have a good grasp of their specific compliance requirements to really gain an edge over their competitors.
That said, one of the best ways to start with compliance is by undertaking a rigorous pre-assessment of the design of your product against the applicable international standards. A TÜV Rheinland report mentions early compliance checks as one of the means to reduce the risk of redesigns-with about 20% of the overall production costing part of the problems-induced by such redesigns. Besides, utilizing local knowledge by engaging certified compliance consultants should reveal some region-specific priorities that might otherwise be lost.
Manufacturers should also use comprehensive compliance management software capable of monitoring changes in international regulations. According to the Compliance Gifts Group research, companies that use such digital tools face as much as 30% fewer issues with compliance. Organizations can not only suffer reduced risks but also boost their reputations in international markets by establishing an efficient compliance process and ensuring the very latest knowledge of regulations. With increasing measures of compliance being enforced throughout the world, such an approach is even a strategy in itself to stay ahead and maintain growth sustainability.
Future Trends in Electrical Standards and Compliance in Manufacturing
Within the manufacturing sector, with vast development simultaneously occurs the electrical standards and compliance sector that is beginning to witness great change. Reports from the industries suggest that by 2025 nearly 75% of manufacturing firms will have put advanced applications such as IoT and AI in place, thus creating the necessity for more socket tests to be performed. This transformation involves not only the aspect of innovation but also the ability of all-new technology to be put against already established and future regulations to fill up a critically grievous gap in global manufacturing compliance frameworks.
Another major issue cited in current studies is the phenomenon of harmonization of electrical standards across regions. The International Electrotechnical Commission (IEC) mentions that there has recently been a 20% increase in regional agreements that seek to unify electrical compliance standards, great news for manufacturers that operate in more than one jurisdiction. These harmonization initiatives try to alleviate the burden manufacturers have due to varying local regulations when it comes to market access, so they can pour all that energy and time into innovation, instead of compliance hurdles.
On top of that, the concept of sustainability has advanced into a new compliance benchmark in manufacturing: 65 percent of manufacturers put emphasis on energy efficiency regarding design and components as their best practices in keeping with the environmental standards of today, according to the report by the Global Manufacturing Coalition. This is indicative that electrical standards must now cover safety, performance, and also sustainability. As regulations evolve to incorporate greener practices, manufacturers must stay one step ahead to ensure that their processes meet the new compliance standard while limiting environmental impact.
So, with heavy-duty technological advancement, the future of electrical standards in manufacturing is promised to undergo new and significant adaptations, asking for increased global standardization and focused attention on sustainability. Manufacturers must thus stay ahead of the curve in their dealings with these issues to keep in compliance and remain competitive in the rapidly changing global market.