- Home
- News
Understanding Safety Standards for Visual Checks on Electrical Equipment and Best Practices
Safety and reliability of electrical equipment are highly significant in this modern industry. According to the National Fire Protection Association, more than 20% of fire accidents in workplaces are attributed to electric failures, which calls for effective safety measures. Safety inspections of electrical equipment mostly contain visual checks, through which maintenance teams can nip issues in the bud before they develop. The latest report from the International Electrotechnical Commission (IEC) indicates that regular visual inspections can save up to 30% of equipment failures thus verifying their effectiveness.
Visual checks for electrical equipment are guidelines for any organization that wants to implement safety practices and compliance within its environment. OSHA recommends a systematic inspection of such because it is known to significantly reduce electrical accidents and improve the overall safety of the workplace. Knowing these visual inspections is necessary for compliance with industry regulations and for a safety culture among employees. This article will look into the details of visual inspections of electrical equipment and give best practices to apply concerning creating a safe and productive environment at work.
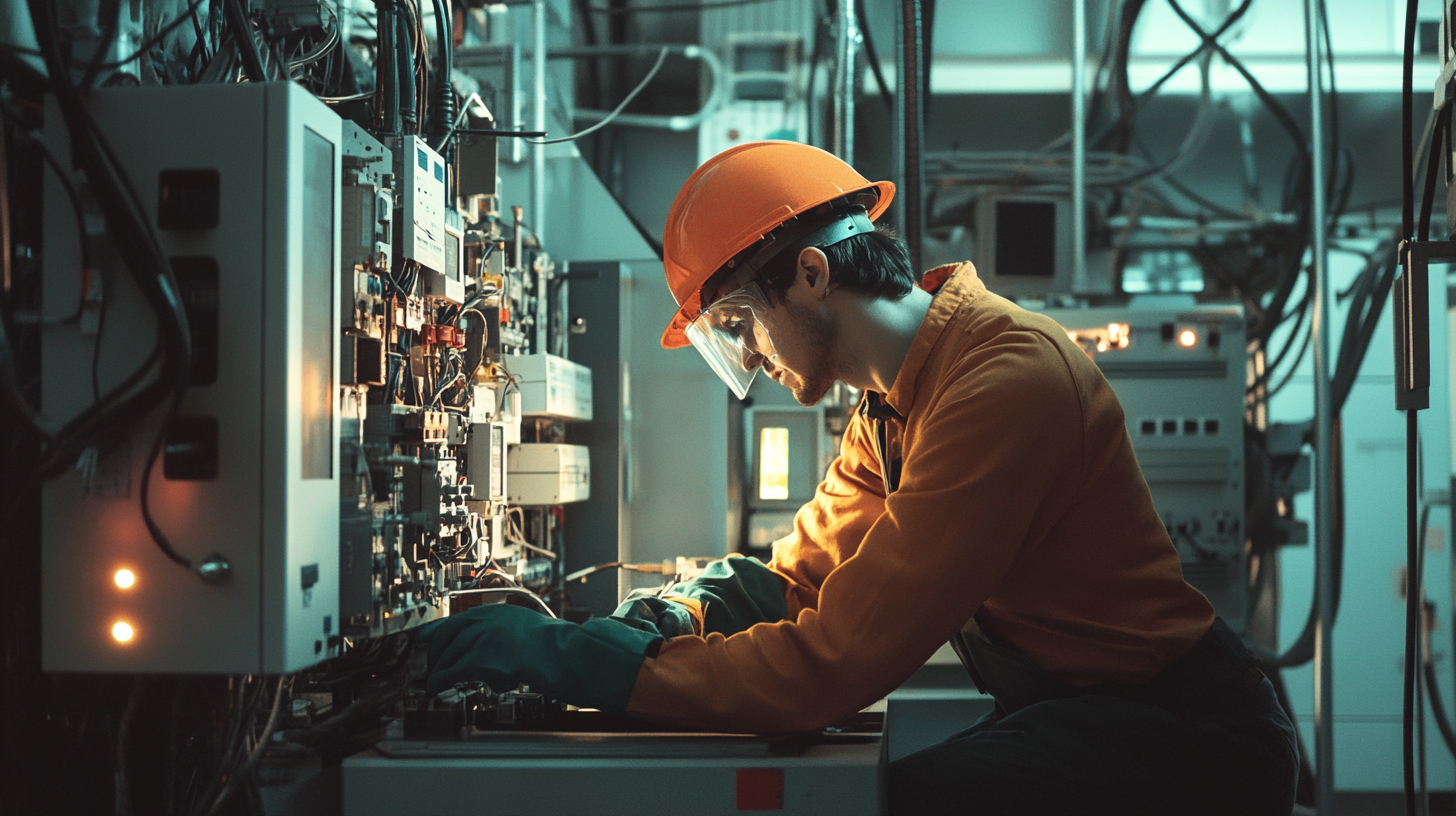
Importance of Visual Inspections in Electrical Safety Standards
Visual inspections are key to electrical safety standards and are the first line of defense from potential hazards. As the NFPA estimates, about 48,000 home structure fires annually are due to faulty electrical equipment, which speaks to the necessity for preventive visual inspections. Regular visual checks help spot early signs of wear and tear, such as a frayed cable, loose connection, or overheating incidents. Considered seriously, these inspections can become vital, occasionally preventing minor problems from developing into safety nightmares. According to a study by the Electrical Safety Foundation International (ESFI), nearly 30% of electrical incidents occur due to improper installation and maintenance, affirming the need for safety standards. Other best practices related to visual inspections include checking for compliance with local codes and standards, consistent inspection programs, and utilizing advanced technologies like thermal imaging for temperature anomaly detection for safety and durability of electrical equipment while also protecting against expensive downtime and maintenance. Including such visual inspections in the regular maintenance protocol will assure that organizations meet strict safety criteria and instill a culture of safety awareness with their employees. Since hazards related to electrical equipment are a major cause of incidents in the workplace, regular visual inspections remain critical in protecting both lives and property. Thus, when visual inspections are prioritized, organizations uphold the safety regulations while adopting a culture of proactive electrical safety throughout their operations.
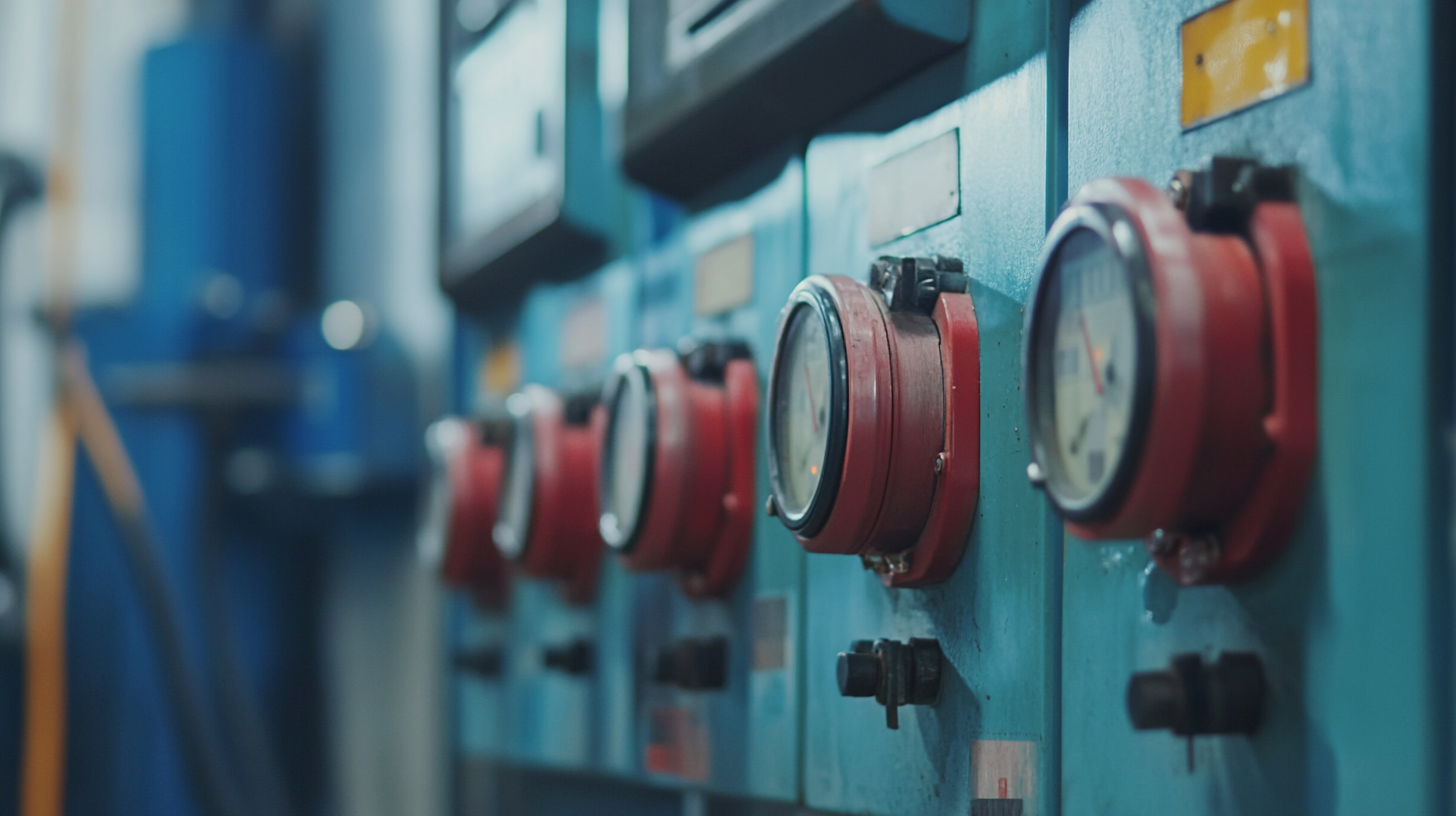
Key Safety Standards Governing Visual Checks for Electrical Equipment
Visual checks of electrical equipment are important in safety and regulation. Several safety standards govern these checks, and understanding standards is a must for any organization involved in electrical installations. The main standards include those promulgated by the National Fire Protection Association (NFPA) and the Institute of Electrical and Electronics Engineers (IEEE). They include very detailed requirements for periodic inspections. These standards spell out the frequency of inspections, listing the visible signs of wear, corrosion, or moisture ingress as part of the inspection elements.
In addition to NFPA and IEEE, certain standards established by OSHA stress the significance of a complete visual inspection regime. According to OSHA, visual inspections should be performed frequently to find any potential hazards concerning electrical equipment. Inspections include things such as checking for frayed wires, loose connections, ensuring equipment is properly grounded, etc. Complying with safe practices can prevent electrical failures and therefore promote safety in the workplace.
Best practices for visual checks are equally important. Organizations are encouraged to provide training for personnel to recognize red flags during inspection jobs. Developing a checklist using the established safety standards may ensure that no crucial area is omitted during the assessments. Tools like infrared thermography can further compliment visual inspections by locating hotspots not visible to the naked eye. When aligned with these primary safety standards, organizations can foster a safe working environment and bring about operational efficiency into visual check processes.
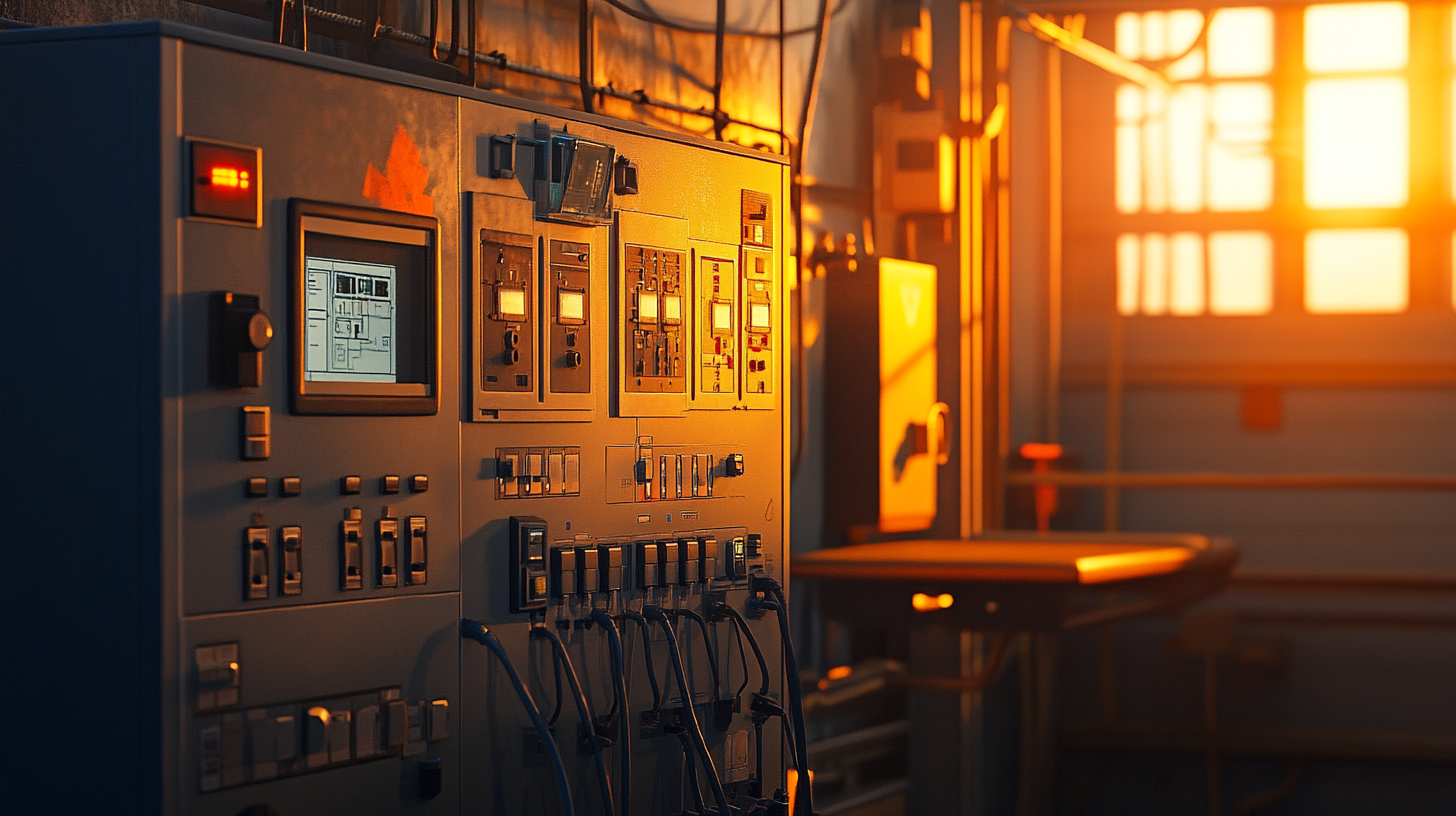
Best Practices for Conducting Effective Visual Inspections
Visual inspections of electrical equipment play a vital role in ensuring the safety and efficiency of operations. A report from the National Fire Protection Association (NFPA) indicates that almost 47% of electrical failures can be attributed to either improper maintenance or visual obsolescence. This stresses the importance of continual comprehensive visual inspections, as they go a long way in identifying hazards before they result in incidents or failures of equipment.
When performing visual inspection it is good to go about it in a systematic manner: pre-inspection checklist condition-could include, but not limited to, insulation checking, correctness of cable management, check for signs of wear or overheating. The American National Standards Institute (ANSI) recommends that such visual inspection be done at regular intervals depending on type and operating environment of equipment. For example, equipment that undergoes operation in a harsh environment should be inspected more frequently, quite possibly quarterly, for early, possible detected deterioration.
Apart from thorough checklist development, advanced technology would call to enhance the performance of these inspections. One such technology is thermal imaging cameras that detect hotspots that cannot be seen with the naked eye. According to the International Electrotechnical Commission (IEC), adoption of modern technology improves diagnostic accuracy and reduces risk of electrical failure by approximately 40%. The organizational best practices when it comes to visual inspection would go further to realize proactive culture of safety and reduce the chances of electrical incidents to quite an extent.
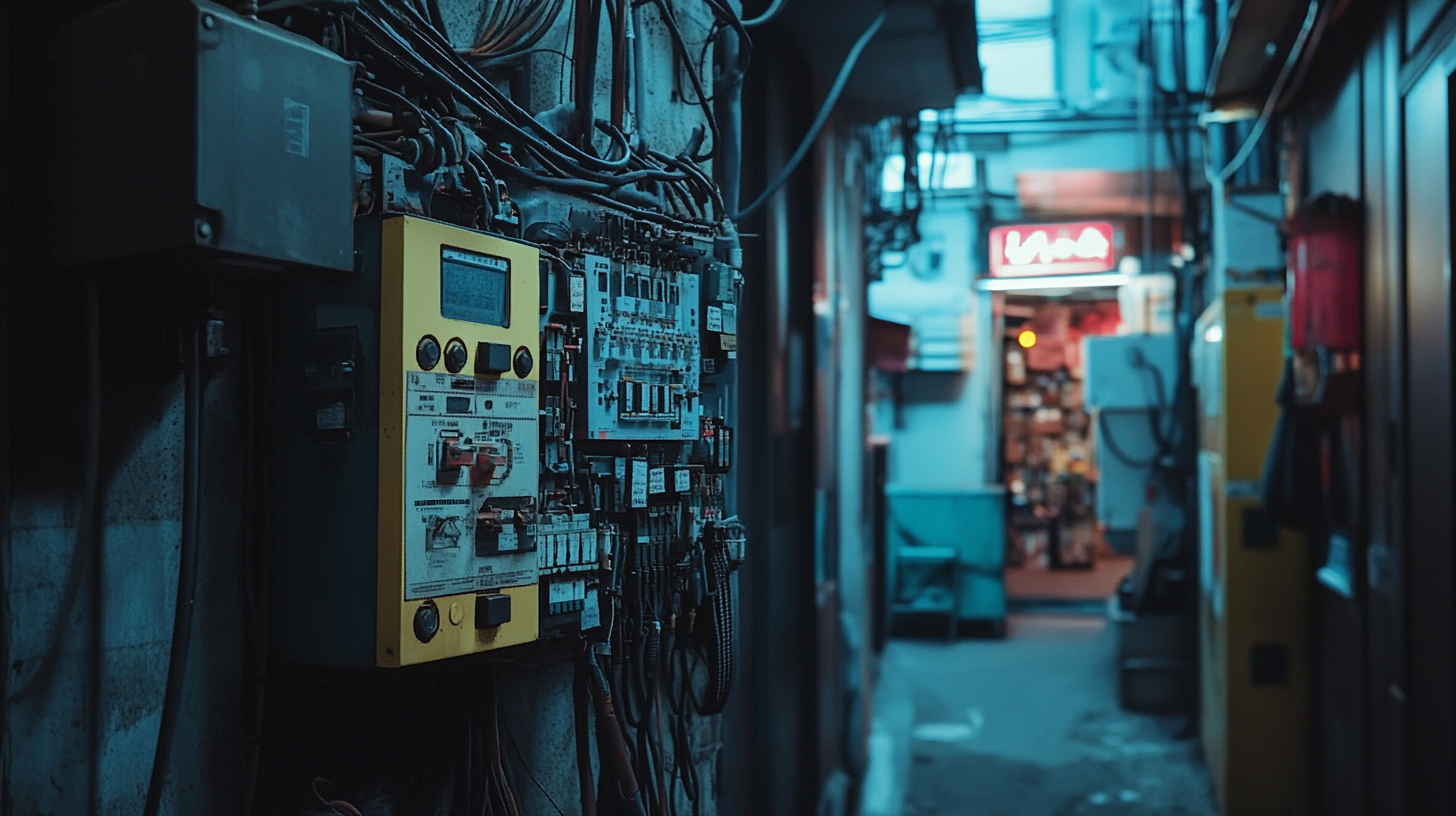
Common Electrical Equipment Issues Identified During Inspections
As far as the upkeep of electrical equipment is concerned, visual inspection constitutes an important preventive activity that assists in drawing attention to possible hazards before they develop into serious problems. Such problems include telltale signs of deterioration, ranging from frayed insulation on wires to corroded terminals. These visual indications can provide clues to the existence of internal electrical faults that may ultimately result in equipment failure or fire hazards if an immediate response is not called for. Regular visual inspections allow for further opportunities to address the onset of these problems with great diligence, thus guaranteeing the safety of the equipment and the place of installation.
Overloading outlets is another very frequently observed problem during electrical inspections. An overload puts a stress on the electrical systems, leading to overheating and a greater chance of malfunctioning. Inspectors tend to take notice of how many devices are plugged into a single outlet and advise that such a load should be shared more evenly across several circuits. Outdated or improperly rated extension cords present threats in their own right: the inspection should thus consider such cords and compare their specifications against that of the equipment in question.
It's also essential to check circuit breaker and fuse conditions for safety purposes, and inspectors frequently find these components tripped or otherwise tampered with. Proper working condition for circuit breakers and a fuse rating matching the designed load are two critical points that need to be achieved to avoid overload conditions. Remedial actions on these identified common issues during visual checks will form the basis for a safe facility and improved life for the equipment.
Training and Resources for Enhancing Visual Inspection Skills
Inspection or rather visual inspection is one of the key safety measures for electrical equipment; therefore, it is most important to improve these skills mainly by designing training programs for visual inspection that would enable the technicians to assess any potentially dangerous conditions more effectively. Such kinds of programs usually cover several topics from basic electrical safety principles, through the sense of equipment labeling, and often end with the identification of damage and wear indicators.
Out of formal training events, there are volumes of resources available for continuously supplementing education in visual inspection techniques, starting from online courses, webinars, and industry publications to give valuable information on updated safety standards and best practices. Moreover, many companies conduct field-based hands-on workshops to make it possible for participants to practice their skills outside the classroom and at the actual place of work. All this learning helps develop sharp visual inspection skills, further ingraining safety standards delivery as a process and culture in organizations.
Fostering safety culture at the workplace is another thing. Bringing team members together to share previous experiences or lessons learned during visual inspection brings a collective learning effect. The latter has proved to work best by having an environment so that all possibilities are welcome to asking questions and learning more. In this way, all employees would remain alert and informed. An organization will improve its visual inspection capabilities by applying training and creating a safety culture, thus bringing about quality improvement in electrical equipment maintenance outcomes.